Deliveries - declaration and return of material from the warehouse
Introduction
The document describes the mechanism for generating the return of items from the warehouse to the supplier. This can be applied to leased items, i.e. items that are delivered and which we have to return after a certain period of time. These can be formwork elements (this example is based on them), but also drums and additional elements that we have to return.
We want to return the following items from stock. These are the three items that should be returned.
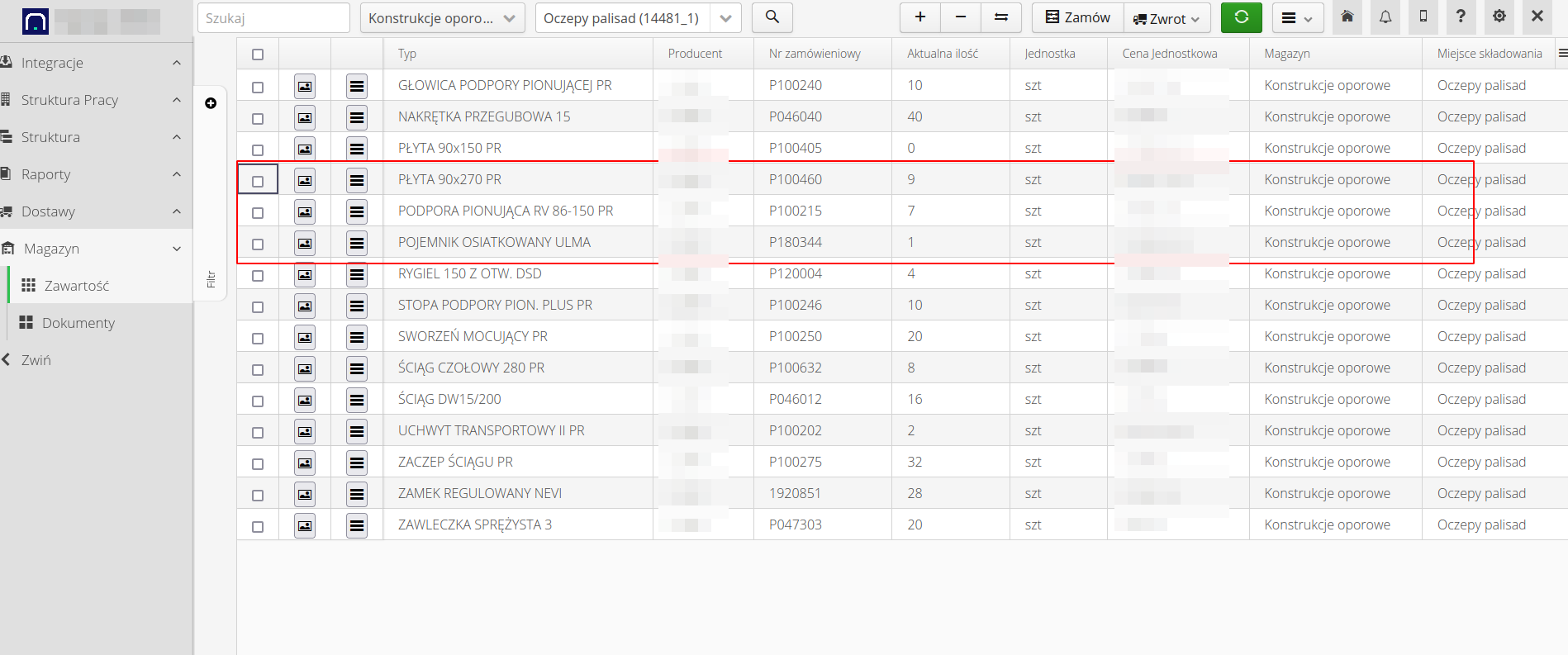
In order to do this, the supplier must provide their cars on which we will load the returned material - we must notify them of this. Then we will load the material and indicate what has been loaded. The next step is to verify the material in the supplier’s warehouse. This can be done either manually or by using automated integrations with the supplier’s IT systems.
Return declaration
-
To start the return, select the warehouse, choose what you want to return and call the return order declaration action. We can also add items to an existing (and open) return order from other structural items.
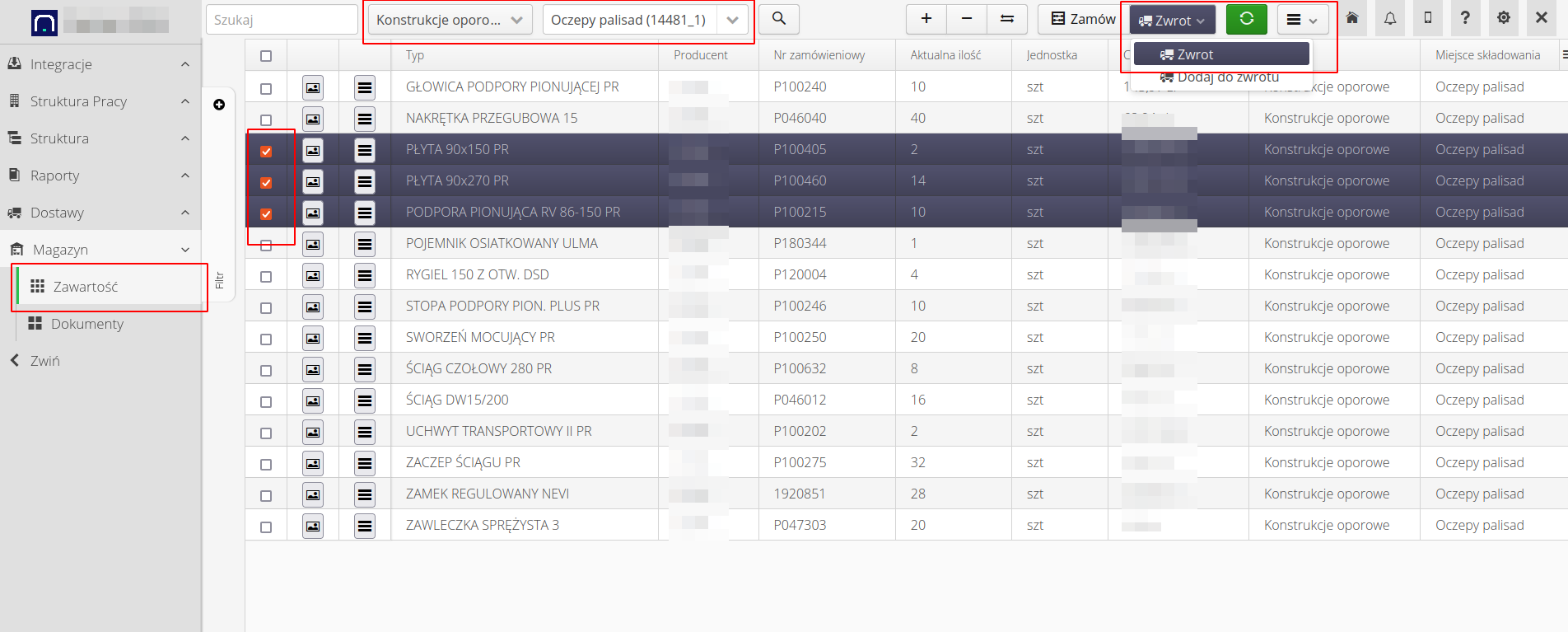
Selection of items to return is optional. We can also create an empty return order at the structural item (work order) level with only specifying the number of vehicles we need to load the return. |
-
Enter the description of the return order - we describe the scope for information, we can modify the quantity of returned items (by default, the total quantity in stock is taken). We save the return order declaration. Such a document is sent to the supplier after the status changes to 'Approved'. The supplier can then confirm the arrival date of the transport, etc.
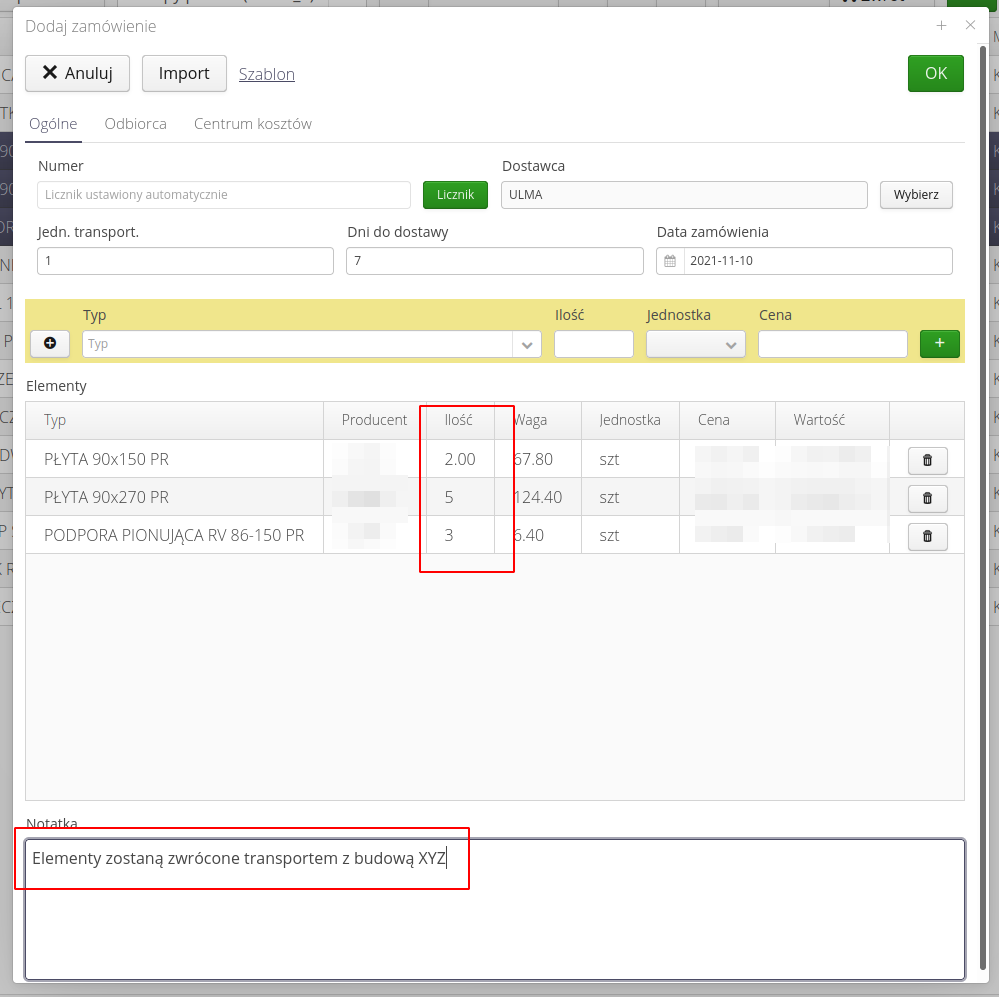
-
Immediately after creating a return order, the system will immediately ask whether to create a physical return for the order. The return itself (for the order) allows you to physically load the elements on the vehicles (when they appear).
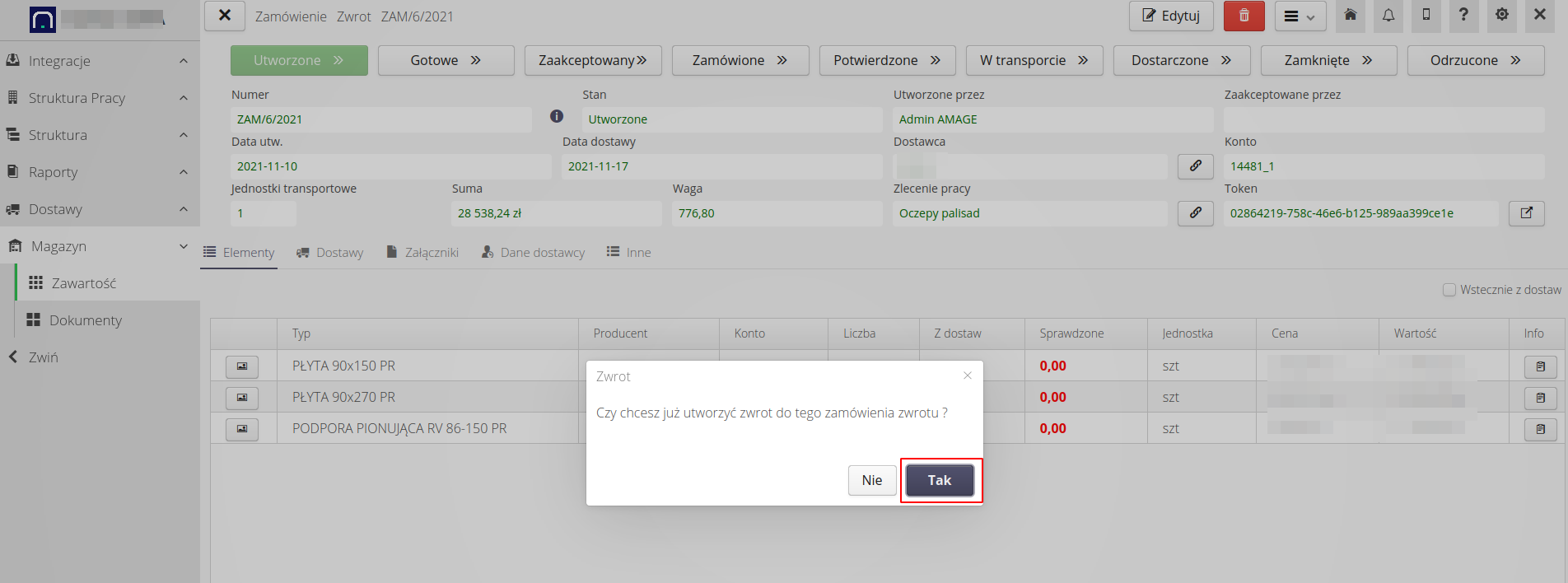
-
The system automatically enters the items specified in the return order into the return. It can also be an empty list and supplement it already during loading at the construction site. We save the return declaration in the system. It automatically receives the status "Loading".
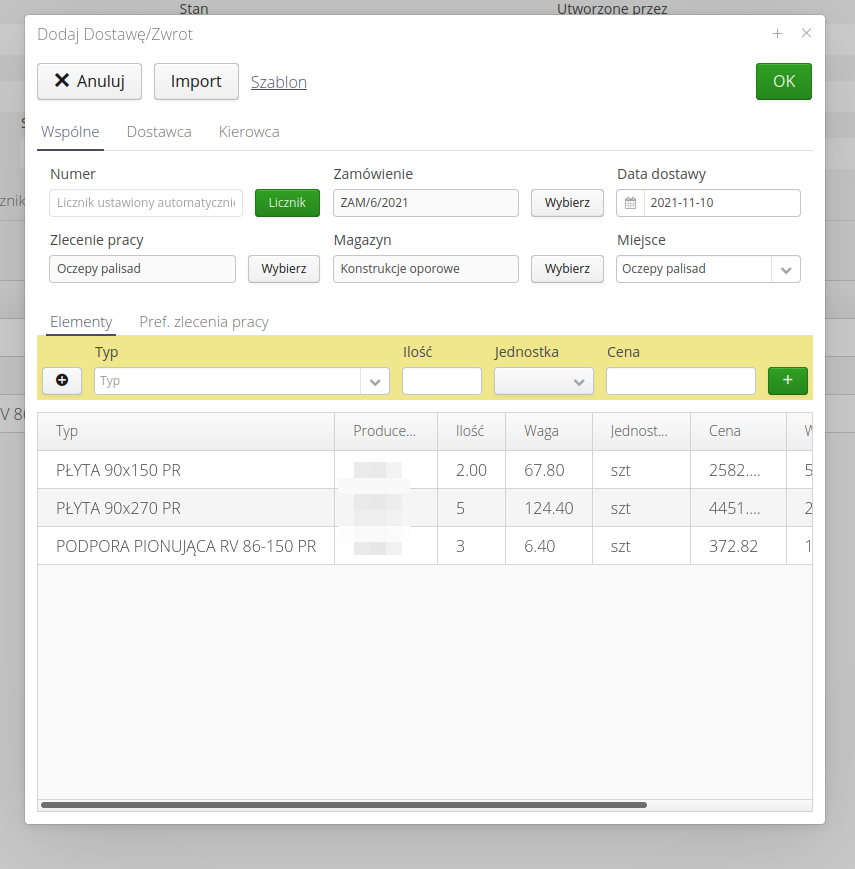
If we want to skip the stage of sending the return order to the supplier, we immediately change the order status to 'Delivered'. In this case, no email will be sent about what we want to return to the supplier. If we changed the status to Approved , the system would send such information and change the status to Ordered.
|
In the details of the return order, we already have information about the declared elements and those that are specified in the loading.
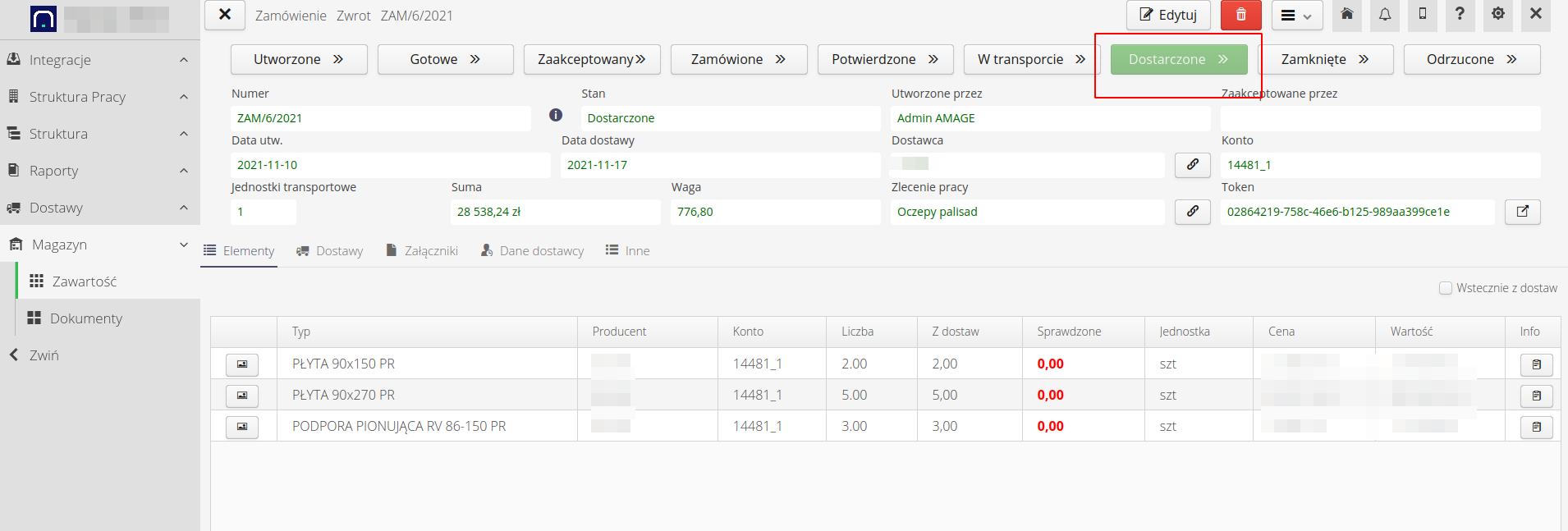
-
In the 'Delivery' tab, we can see the declared return in the 'Loading' status
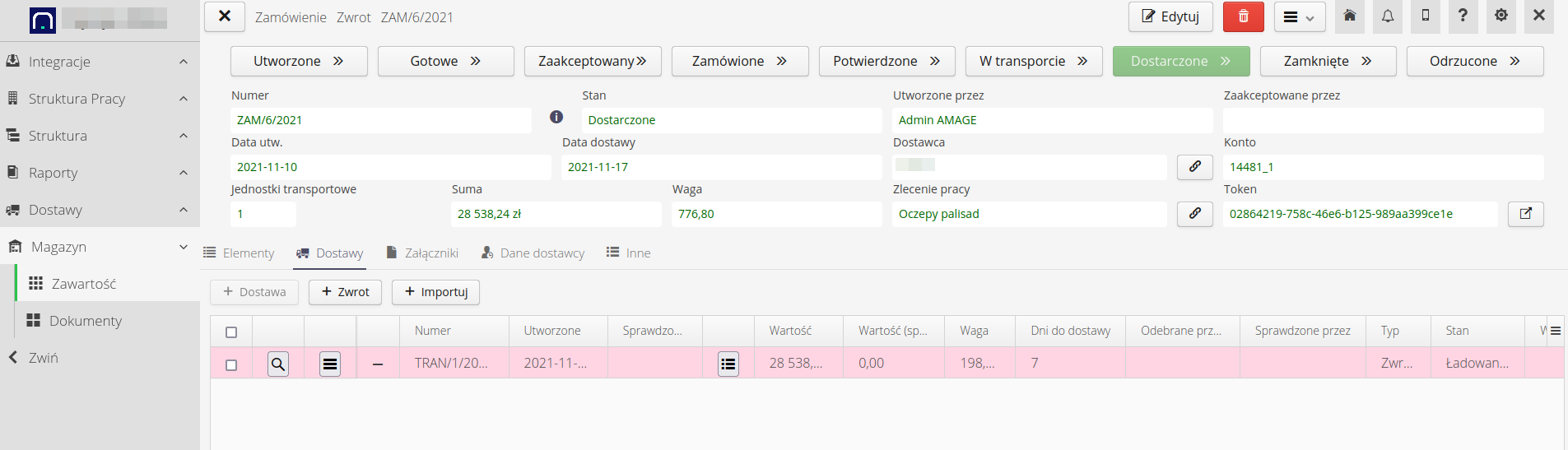
-
We move on to the details of the return. It is here that we have information about which elements have been loaded, which ones have been declared on the basis of the return order. To carry out the loading, we can either open the mobile device, in which we will see the given return in the section Deliveries/Returns and we can load there (directly at the construction site). We can also trigger the loading directly from the desktop interface from the return context menu.
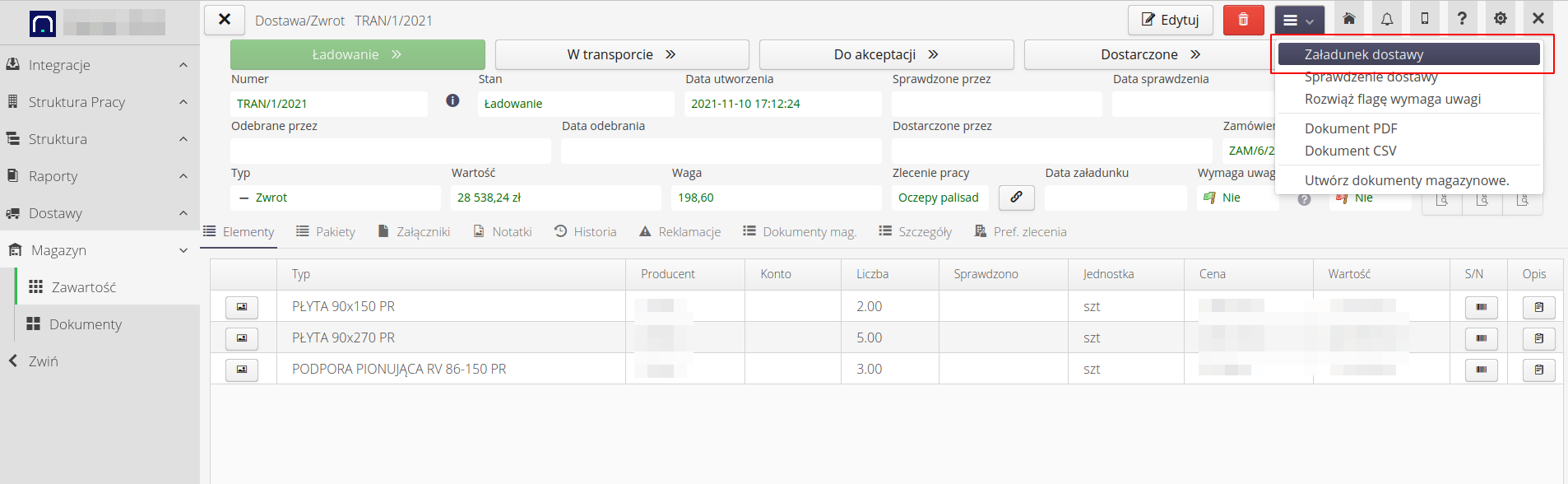
Availability of loading/checking depends on the status of a given document. If we have the Loading status, we can perform the loading operation.
|
-
The loading window opens. Depending on the configuration of the instance, we may be able to indicate loaded items. By default, all elements from the declaration are loaded. We can specify the number of loaded items. We can also add items based on stock levels. We can also add photos/captions to the upload.
-
Alternatively, depending on the configuration, we can indicate the structural elements of the order and determine their order in which the supplier will settle the returned elements.
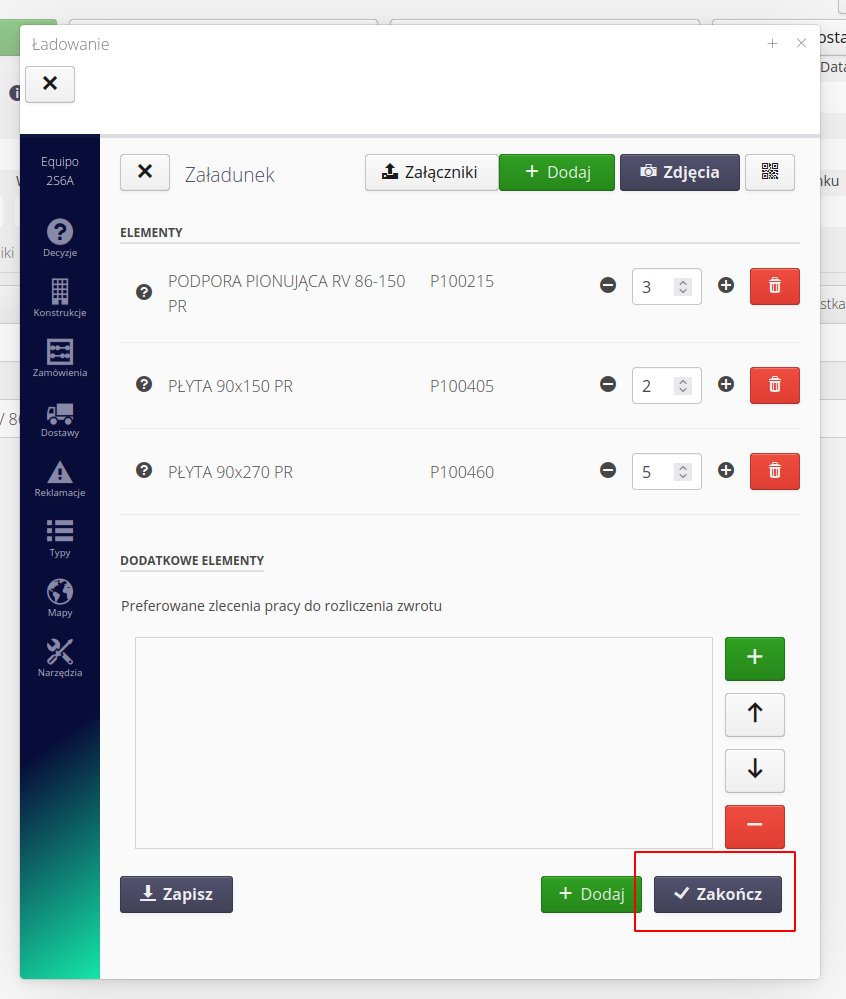
The system periodically (every 30 seconds) saves the loading status. This allows you to avoid losing too much data in the event of a lack of connection to the server, phone discharge, etc. |
-
After confirming the loading of the return document, the status changes to 'In transit' and an email is sent to the supplier with information on what items have been loaded and sent to the supplier.
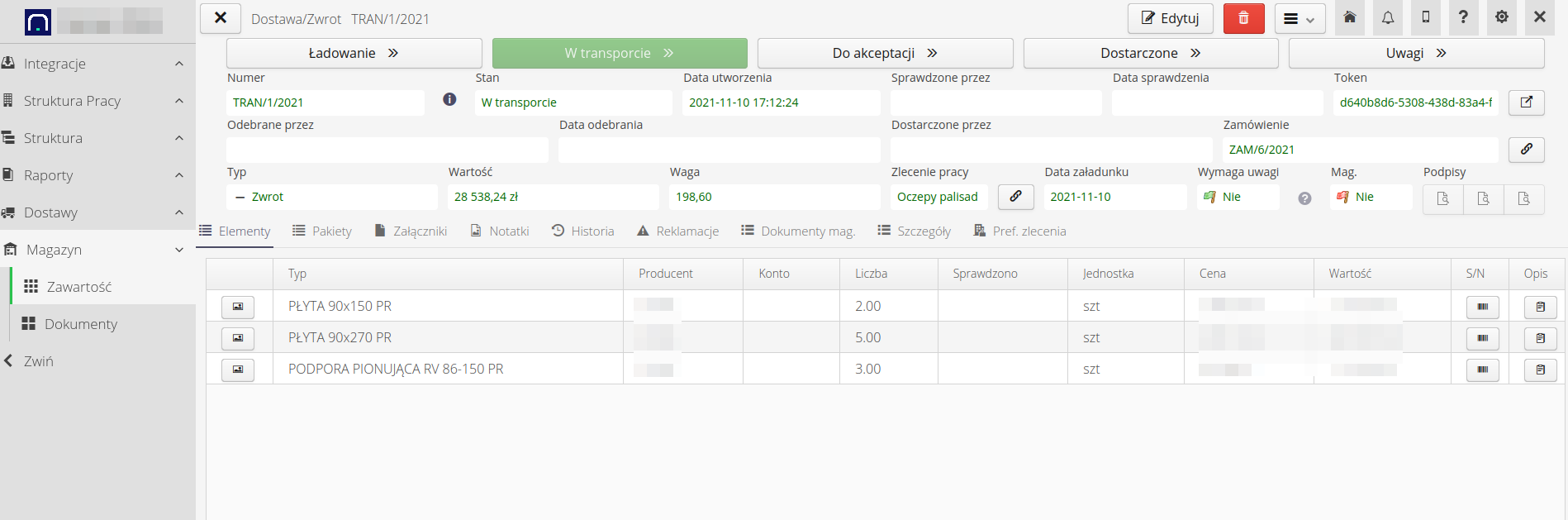
Further steps:
-
In the case of automatic integration of IT systems with the supplier, we may receive a return check in the form of the supplier’s GRN document. In this case, the supplier verifies the returned items and sends a document that we treat as a return check (at the supplier’s warehouse)
-
In other cases, we can perform the check ourselves (mobile or desktop)
Manual return check
-
The return is in the status "In transit". We invoke the return check from the document’s context menu.
-
We can update quantities, add photos, captions, etc. For details of all operations, please refer to the user manual.
-
In this example, we complete the check without changing the quantity, we do not create a complaint. If the user is authorized to perform warehouse operations, a question will be automatically opened whether to immediately enter the document into the warehouse and correct the quantity. If the user does not have such permissions, someone with permissions from the return view can do it.
-
In our case, we agree to put it into storage
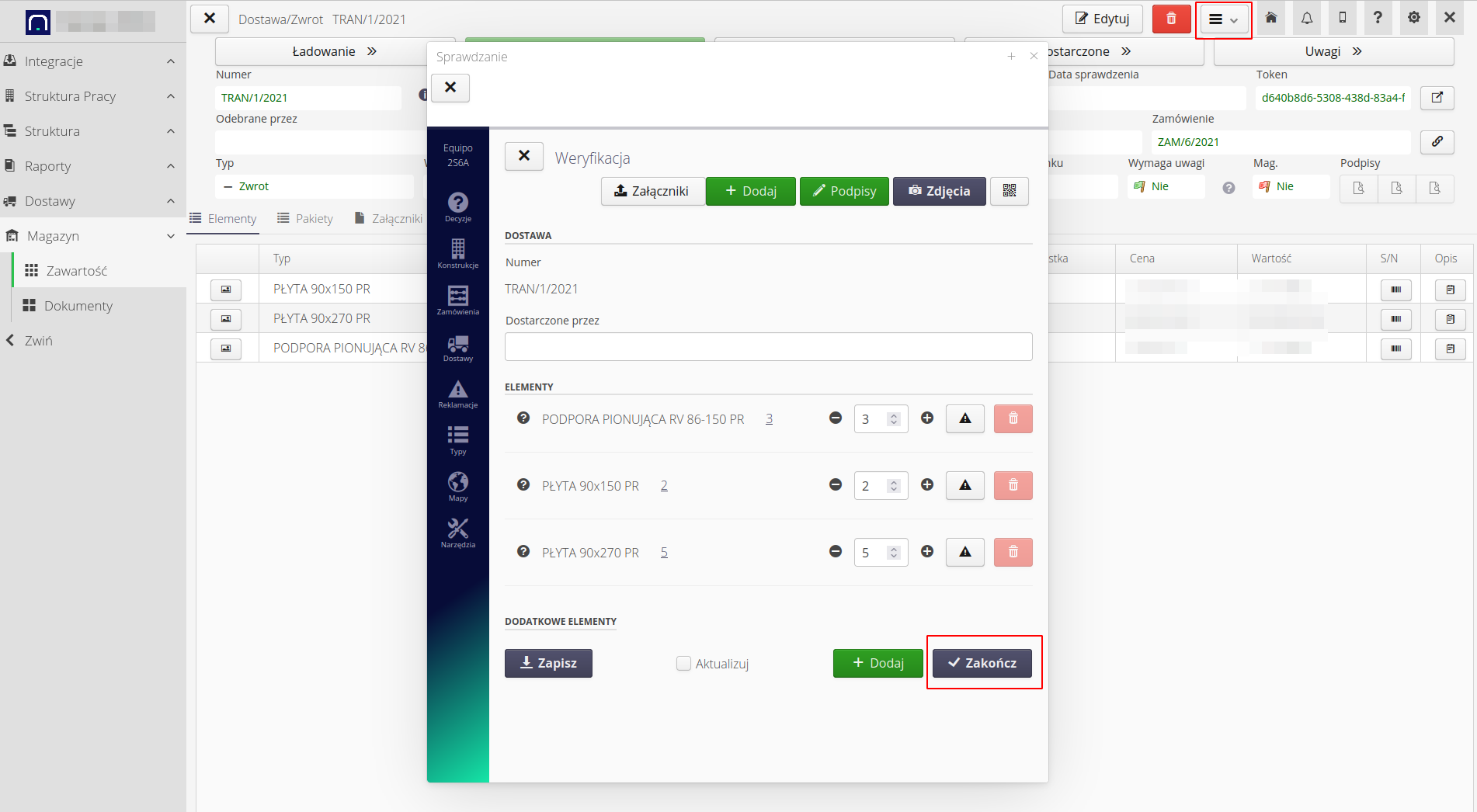
-
We indicate how to number the warehouse document and set the date of entry/removal from the warehouse. After approval, an issue document is automatically created from the warehouse and the stock levels change.
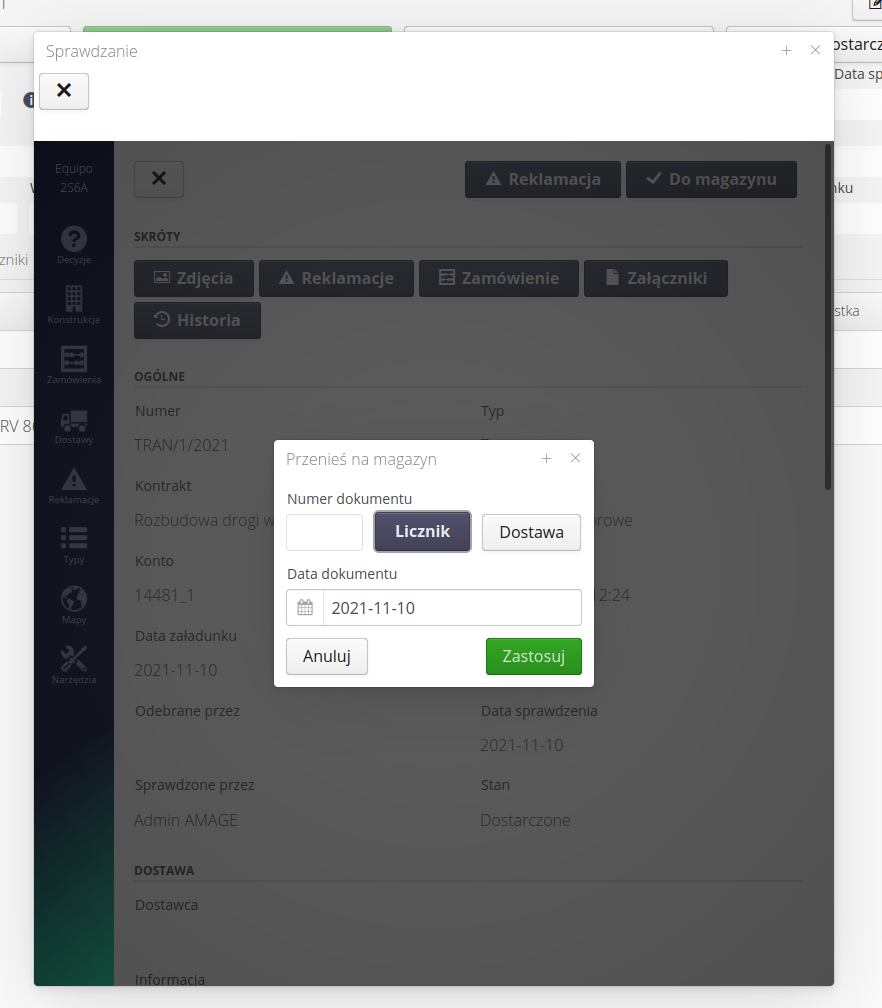
-
The inventory has been corrected. The stock corresponds to the current stock of the warehouse at the construction site. The target documents have been forwarded to the supplier.
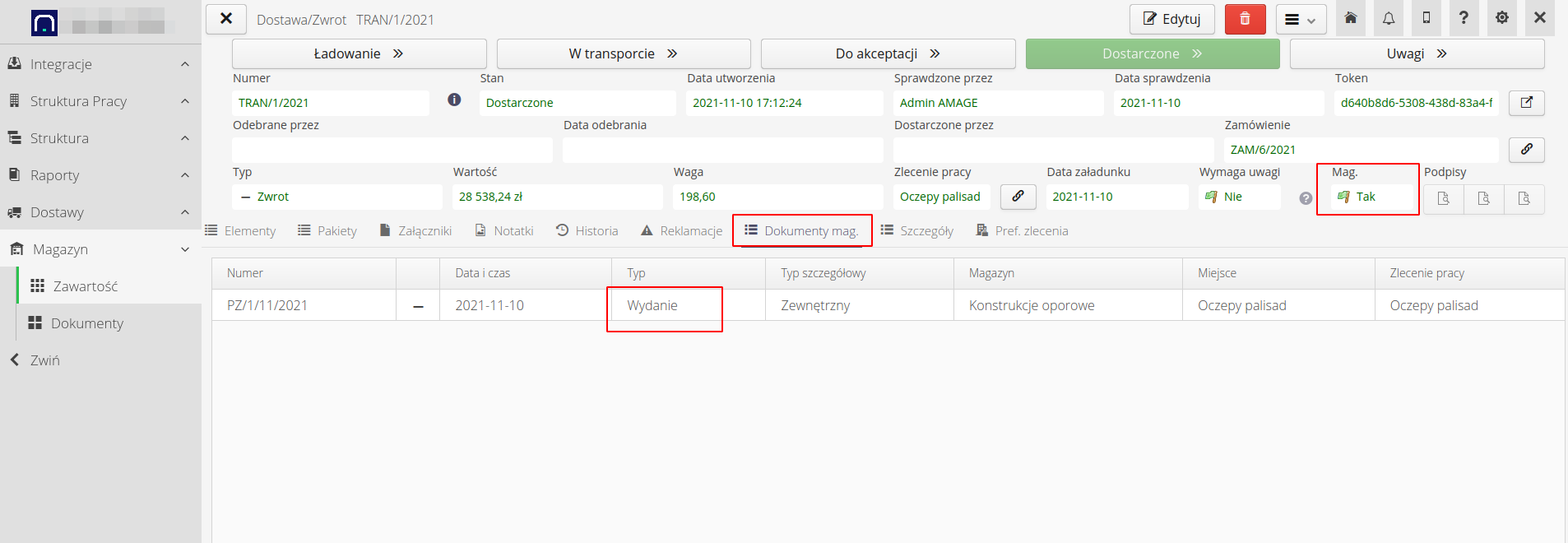
We are finishing the operation. Ready :)
Direct release from the warehouse without the return procedure
If we want to omit the return operation and notification of the supplier (in the default system configuration), we can return items from the warehouse using the basic document of external issue from the warehouse (WZ).
In this case, we omit the entire procedure of loading, checking and communicating with the supplier. To do this:
-
We go to the selected warehouse. Select the items you want to issue (return) and click the
(-)
button, i.e. release from the warehouse
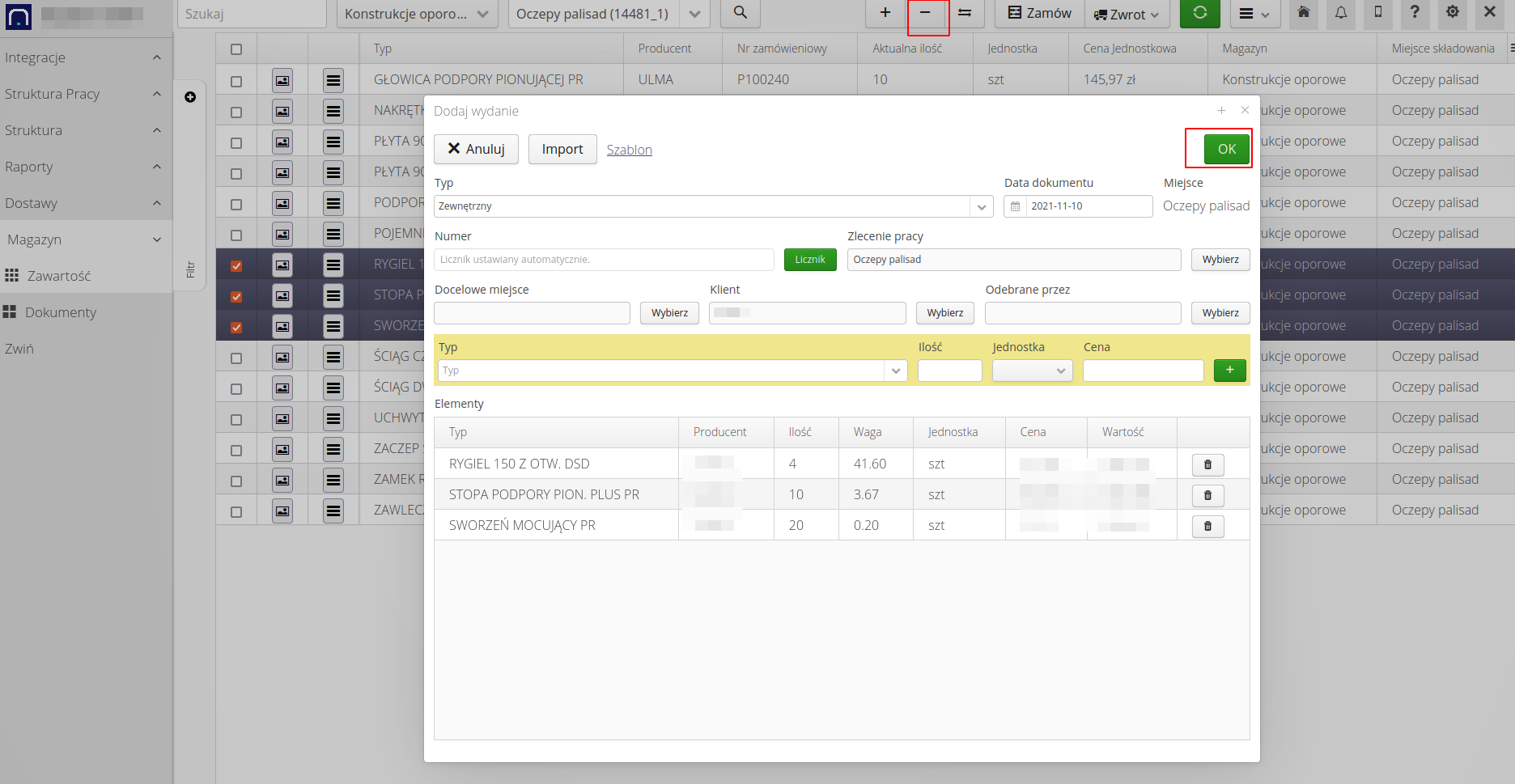
-
We complete the elements, the recipient, modify the quantities, etc. We approve the document.
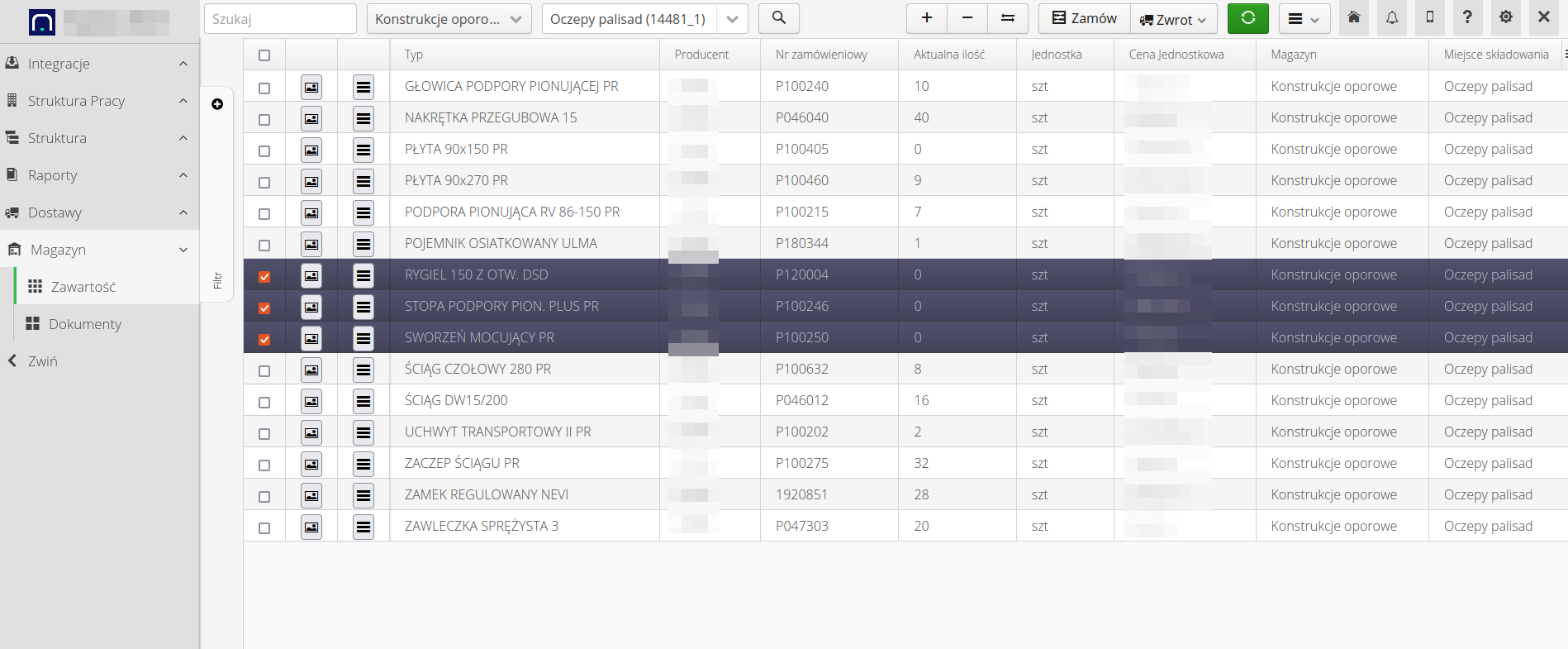
-
The stock level decreases accordingly. The issue document is created.
By default, we do not send such documents to the supplier. This can be configured to upload the document automatically. You can also generate a PDF/CSV WZ document yourself and send it to the supplier as a confirmation of return. |
The Howto is based on system version 1.17.0.2 (03.2022) and presents features that may not be available in your system. Ask AMAGE about making this functionality available. |
Due to ongoing development of the system, some screens or configuration files may look slightly different, but will still retain the full functionality described here. This does not affect the core functionality described in this document. |