Operational management of concrete deliveries
Introduction
Purpose: supervision over orders, deliveries and consumption of concrete for structural elements at the construction site. The document describes the configuration, commissioning and management of the system for coordinating concrete deliveries and settlements of transport and materials.
Description of the solution
Descriptively, the implementation of the required functionality may look like this:
-
The goal is to be able to manage and coordinate transports of concrete to the construction site and, consequently, to manage information about the work done.
-
We start the implementation with the import of the necessary data. Such data can be prepared in the form of excel/csv sheets. This facilitates the initial preparation of data as well as imports and entering data into the system. These data include: a list of system users, the structure of structural elements forming the tasks to be performed, lists of the assortment necessary to carry out the work. In this case, these will be material lists of concretes and their recipes.
-
In this way, we will receive a list of tasks to be performed in the field of concreting a given investment. We can divide them into contracts, objects (e.g. buildings, floors) and detailed works that we want to monitor. With the help of these orders, we will know about the implementation of works and the status of their implementation. These orders may also contain information about concrete deliveries specific to a given structural element.
-
Each task has its procurement plan. It is a material list specifying information on concrete mixes necessary for the execution of a given element. From these lists, you can initiate a work order with the delivery company.
-
Order plans can be activated both individually for each construction element and collectively for a set of construction elements that have been selected, e.g. After selecting the items, we can create an order for the delivery company.
-
The order is in an editable state at the time of creation. In this case, you can add additional information to the order, such as the type of required pumps, contact information, additional information to be implemented.
-
After changing the status of the order to "Accepted", the system can automatically process such an order into a PDF document (including the electronic signatures of the ordering party) and send it to the specified e-mail addresses to the supplier.
-
OPTIONALLY, a link to log in to the so-called supplier portal. In this case, the supplier can use this link to enter the so-called 'Supplier Portal'. Using this portal, he can confirm the order and declare deliveries.
-
Deliveries can also be declared by the main user of the system on the basis of a prepared order. Deliveries after creation allow you to track the route of the vehicle (if we have information about the location of the vehicle, e.g. GPS) and carry out the procedure of accepting (checking) the delivery on the spot.
-
The check allows you to determine the target structural element and correct the delivered quantities (if necessary). The final effect is information about the actual destination of a given delivery.
-
After confirming the delivery, the user has the option to enter information about the delivery times. Depending on the possibilities, the system allows either calculating information on transport times, waiting times, construction site times and unloading times using information from the location of the vehicle or using a simplified recording of key times at the end of the delivery (arrival time, construction time, unloading time).
-
All this information is collectively sent to the system and constitutes information for dashboards, reports and analytical information that build the concreting log. Each structural element also includes detailed information about deliveries made for this facility, planned and actual quantities. This allows for effective control of the work in progress.
Initial preparation
At the initial stage, we import data from excel sheets. These data are:
-
List of users
-
assortment (types) such as concrete mixes, auxiliary equipment, etc.
-
list of objects/structural elements
-
material plans for individual elements (list of materials)
The example of imports is described in detail in separate manuals and in the main documentation. Pre-data templates are available that the construction worker fills in and import templates are available that will load all data automatically.
The end result is a pre-prepared system for the implementation of activities.
In addition, during the implementation, e.g. document counters, lists of locations, object maps, etc. are configured. |
Work order management
In the list of work orders - structural elements - we have a list of activities/objects to perform works related to concreting. In this view, we can present them in the form of a list, we can group them into task packages (for easier distribution and planning). We can also specify the employees responsible for the implementation, deadlines, etc. Each order also has its own status (active, on hold, completed), priority and type (user-defined).
We launch a given order and start its implementation.
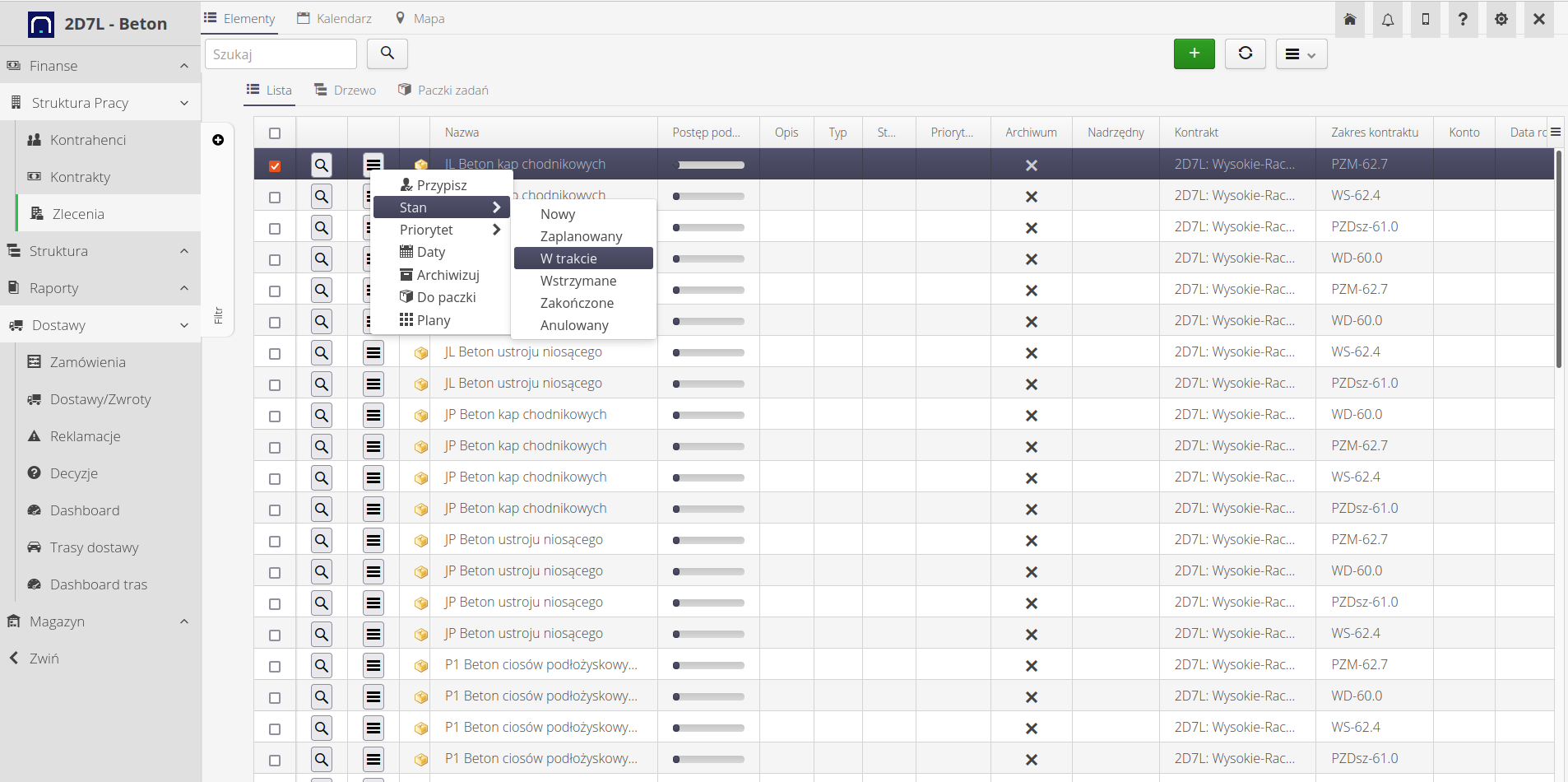
If we have previously imported a material plan for a given element, it is already in the system. If not, we have the option to add such a plan manually in the system. To do this, go to the list of material plans and select the option to add elements to the list.
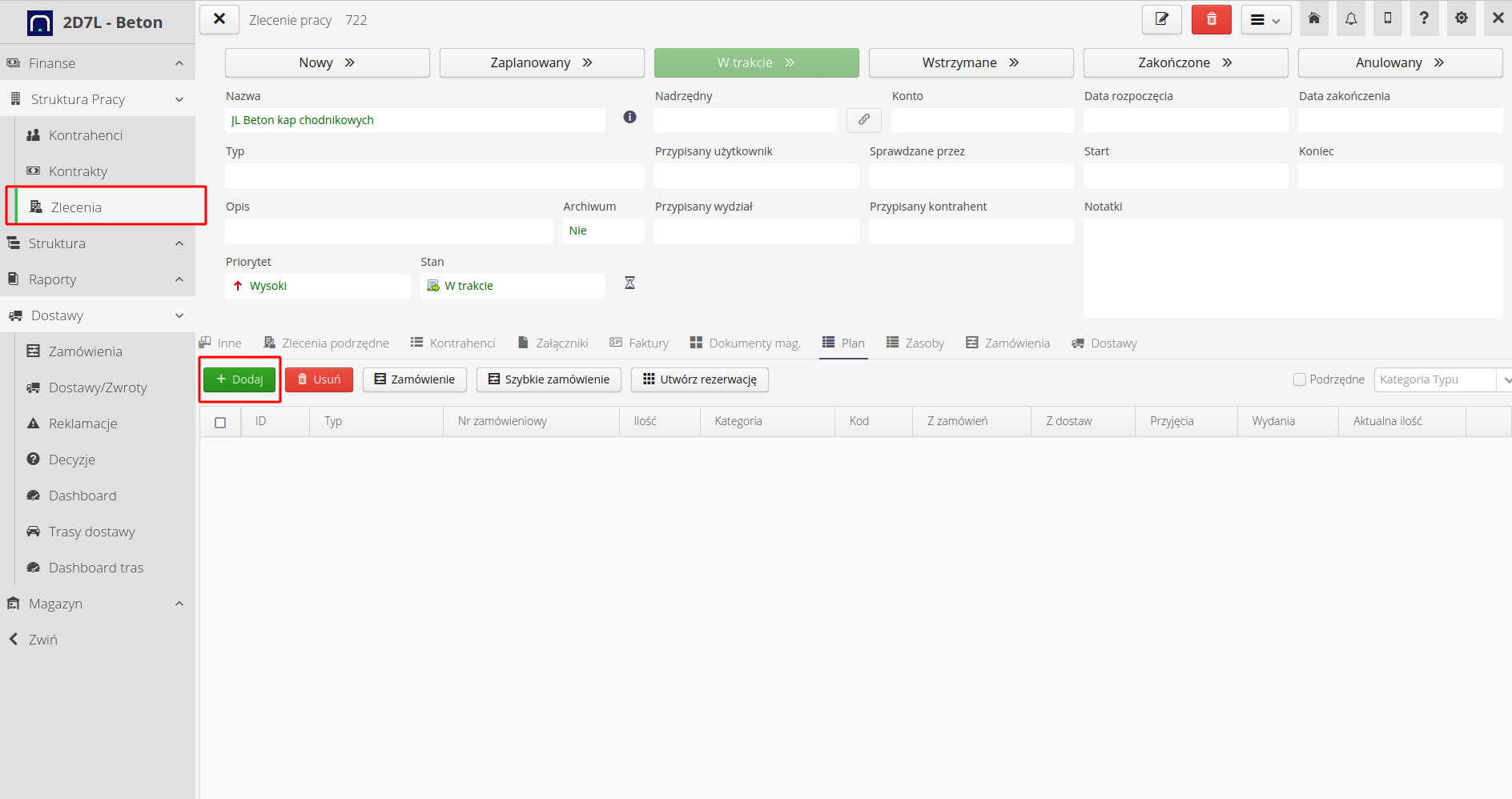
In the definition form, we add elements of the material plan. In this case, we also have the option of specifying additional values that will allow you to search for elements if the material plan is large. Each element can have its own code (additional information that is sent in the order) and a category, e.g. elements of the plan can be categorized in relation to the target function.
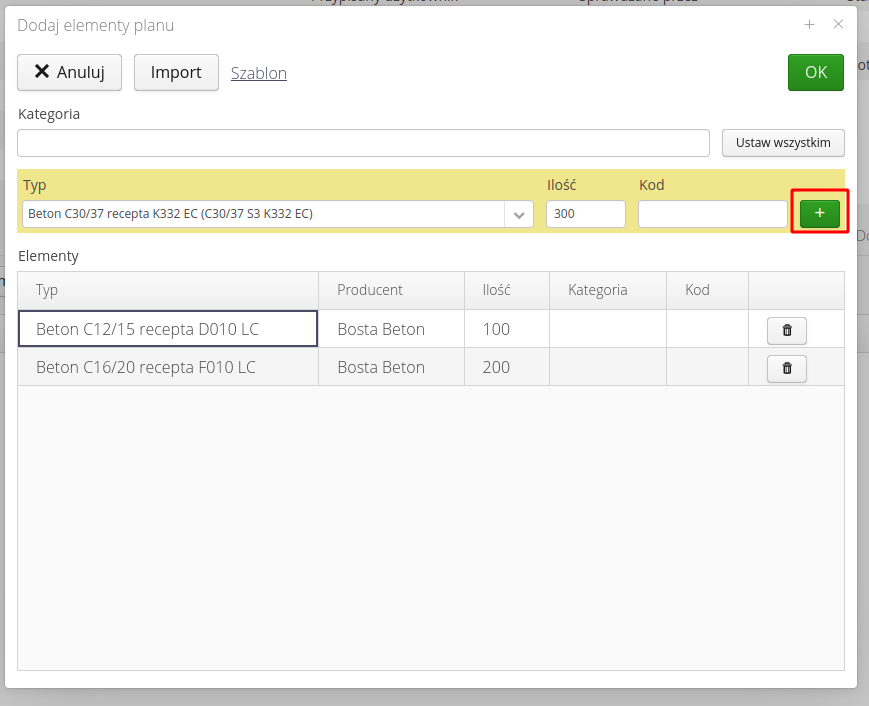
After adding and confirming the material plan, we get a detailed view of the plan. Depending on the enabled modules (deliveries/warehouses), the system automatically indicates information on the planned quantity, the quantity ordered for a given item, the delivered and checked quantity, and warehouse operations (receipts, releases and the current stock level). The system colors the number of elements and stock levels accordingly.
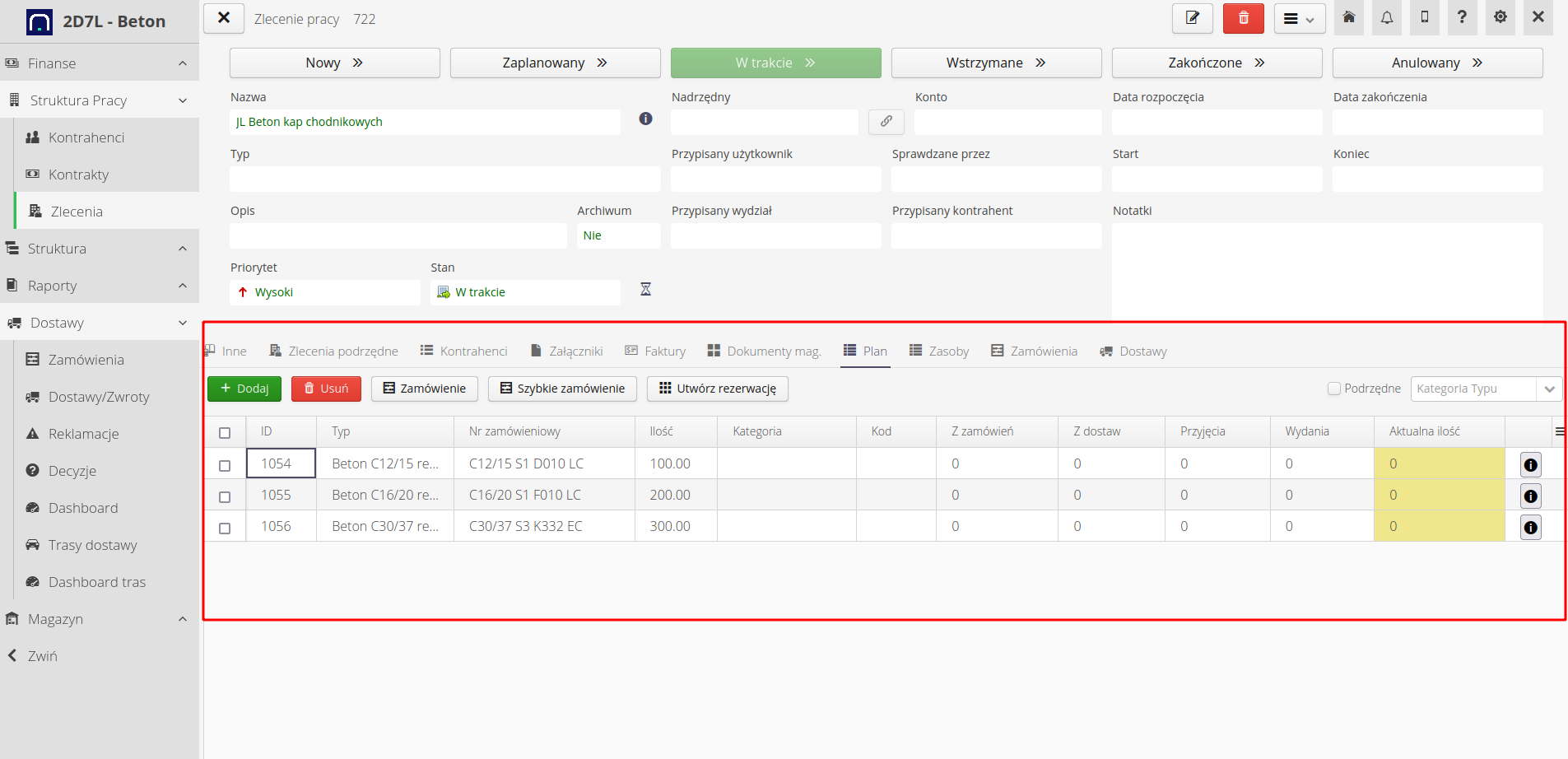
At this stage, we define what is necessary for the implementation of a given structural element and specific material plans. We can go to orders.
Orders from the plan
We can create an order from many places (mobile interface and main interface). This facilitates the generation of orders while working directly on the construction site, but also allows you to plan orders in the office.
To create an order, we can go to the selected structural element and choose what we want to order.
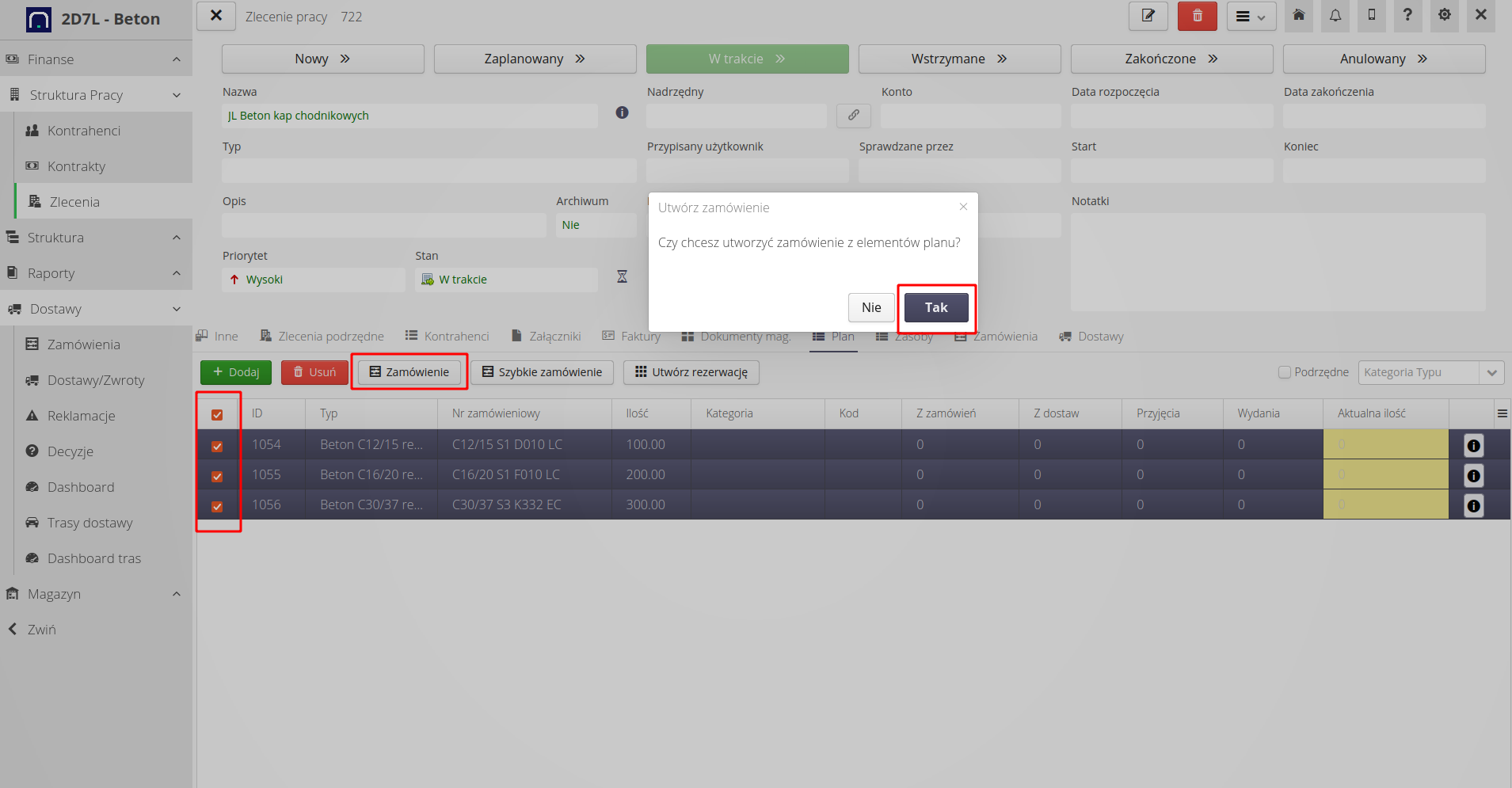
We can also filter selected orders (structural elements) and collectively display a material plan on them and order it collectively.
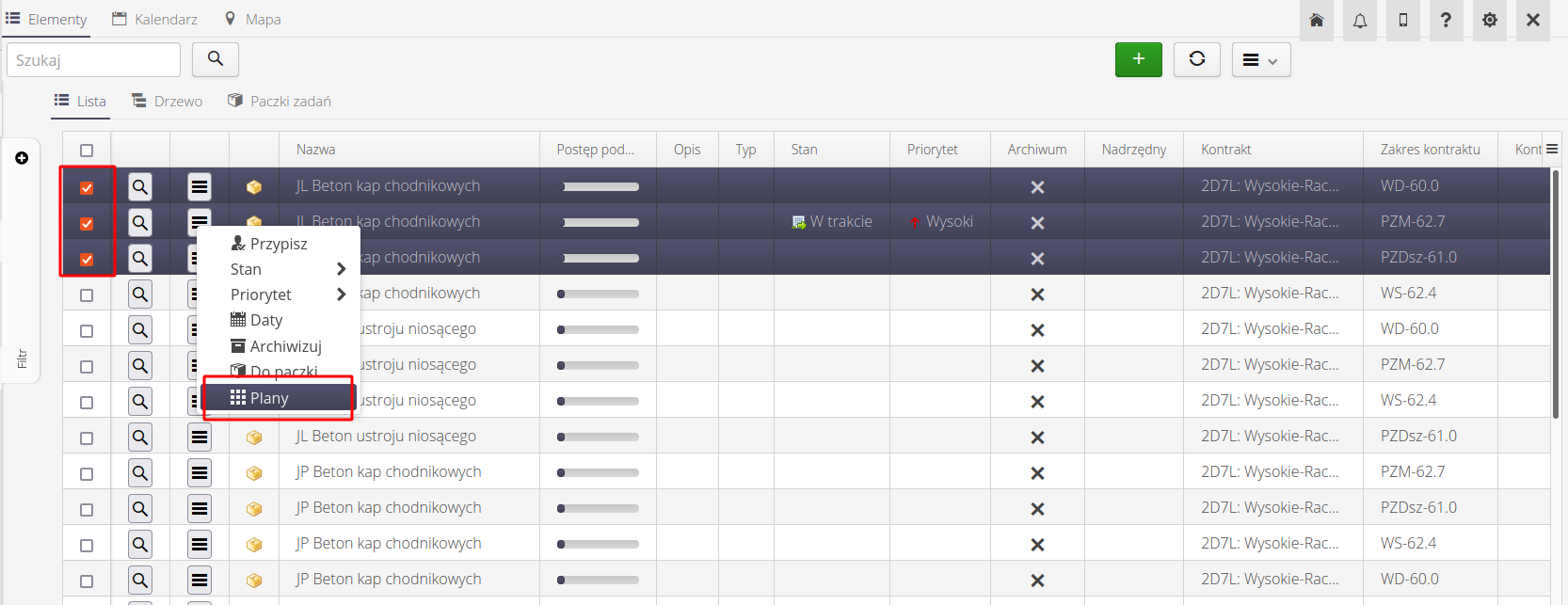
It is always possible to create an order manually and enter all the information manually in the order form. |
In the order form, we complete additional information, select the supplier, comments, and recipients. Here we can also add elements that were not included in the plans, e.g. additional pumps, etc.
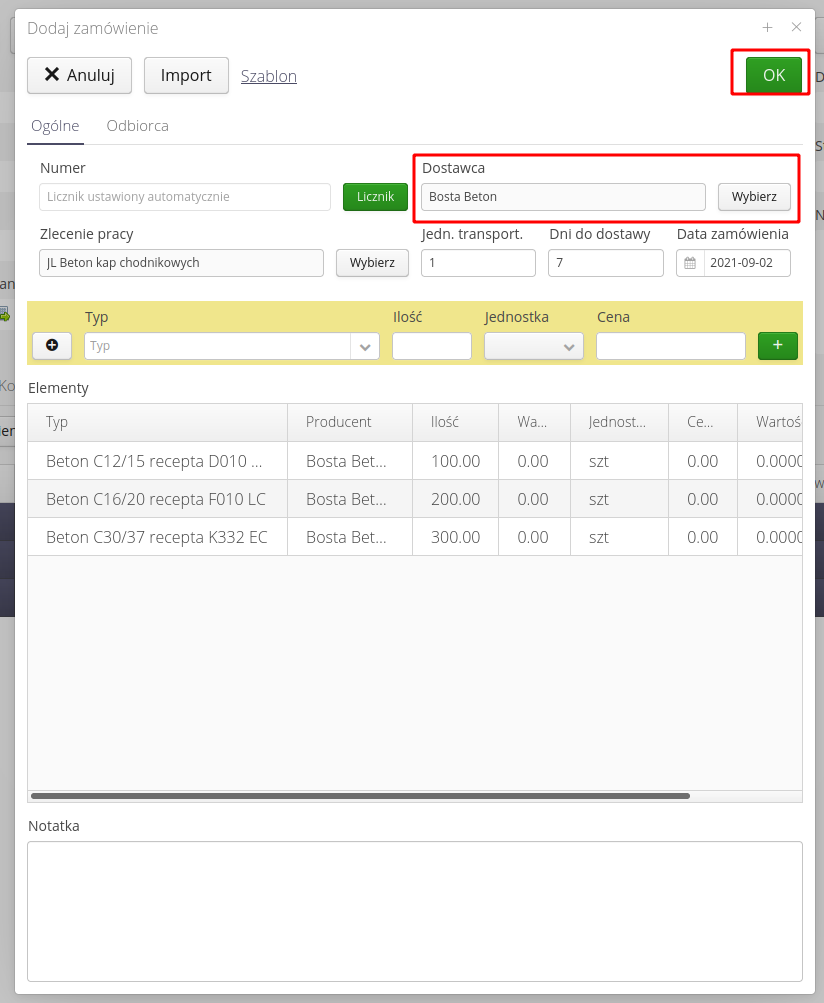
After saving the order, it appears in the list of orders as 'Created' order. This means that the order is being edited and at this point you can still change it, modify it, add elements, etc.
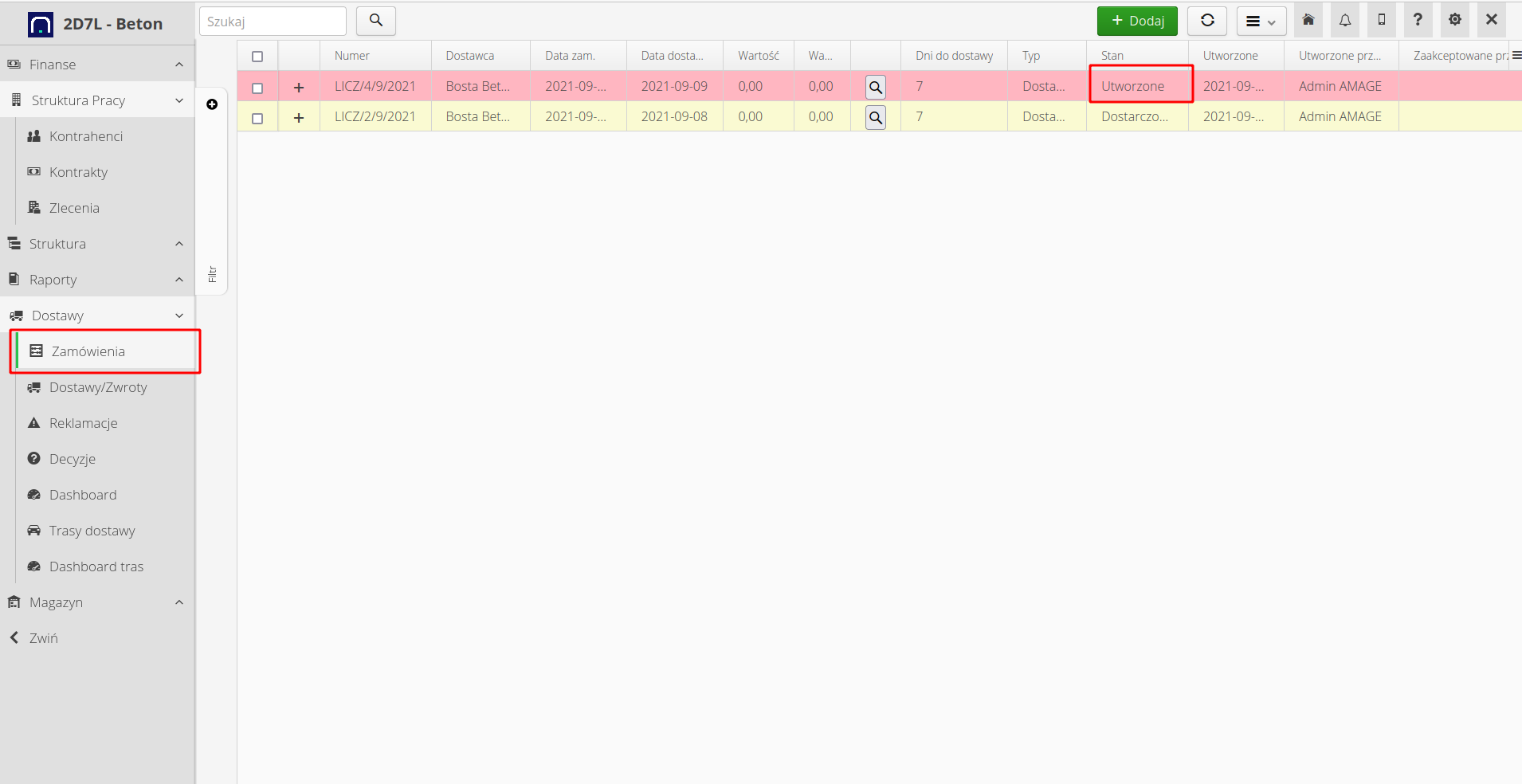
After confirming the order, i.e. changing its status to 'Approved', the system can be configured to automatically send the order to the supplier via email and mark the order as 'Ordered'. The user can always generate an order in PDF form and send it to the supplier himself.
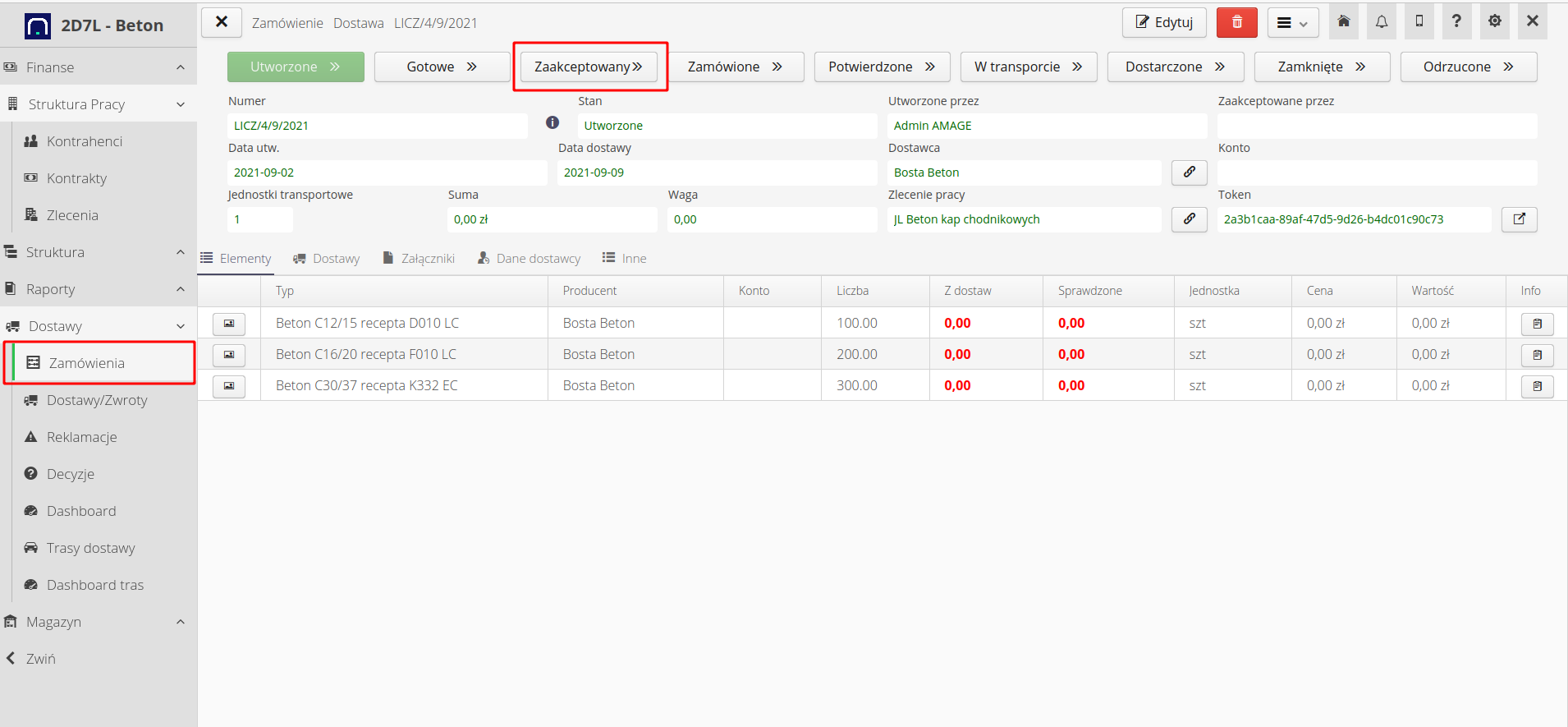
The order, after being automatically sent to the supplier, may additionally contain links to the Supplier’s Portal in the e-mail. A place where the supplier can confirm the order, enter comments, delivery dates and declare specific deliveries with information about the vehicle, driver, etc. |
There is also the possibility of automatic integration of computer systems using delivery-specific EDI formats or generic CSV files sent by the supplier via IT or email channels. |
Mobile work and supply operations
The next step is the delivery. If the deliveries are declared by the supplier via the Suppliers' Portal, the system user automatically receives delivery confirmations. If not, the user can always declare the delivery himself, both in the office and on the construction site.
The mobile system has the ability to define any tiles in the start view. It allows for quick access to individual options and views in the system. To create a delivery on, for example, a phone, select the order link.
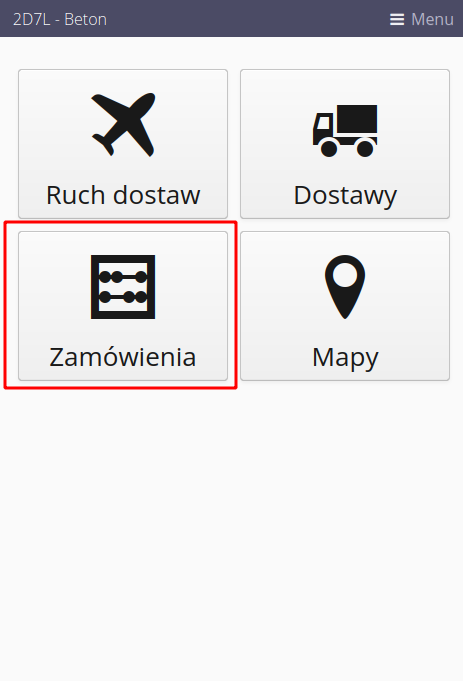
We choose the order. In the detailed view, we can create a delivery based on an order. Here you can additionally modify the content of the delivery (add/remove an assortment).
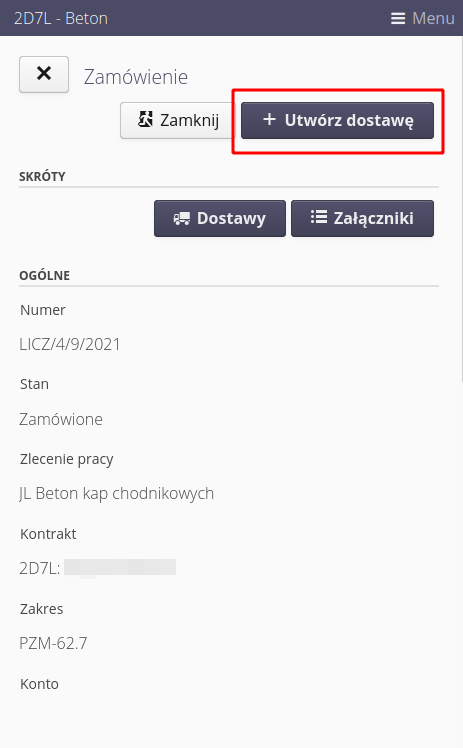
We can also create a delivery via the main interface in the order details view.
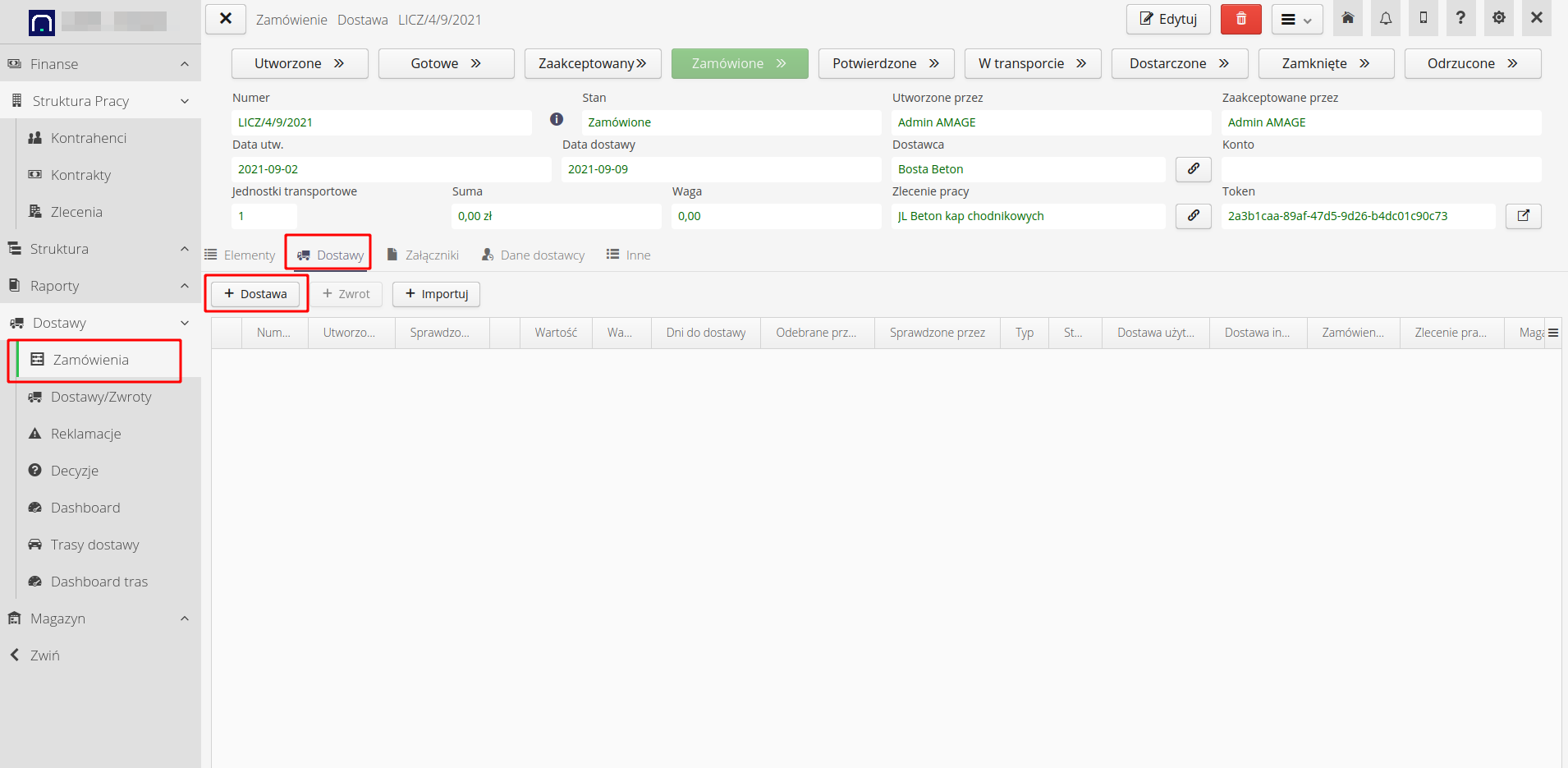
If the delivery is declared (e.g. by the supplier), then it automatically receives the "In transit" status. If we declare it manually, we can also confirm its transport (start of the route) or load it via the mobile interface.
This can be used by users who load at the supplier’s warehouse or by the supplier himself (if given access to the system). |
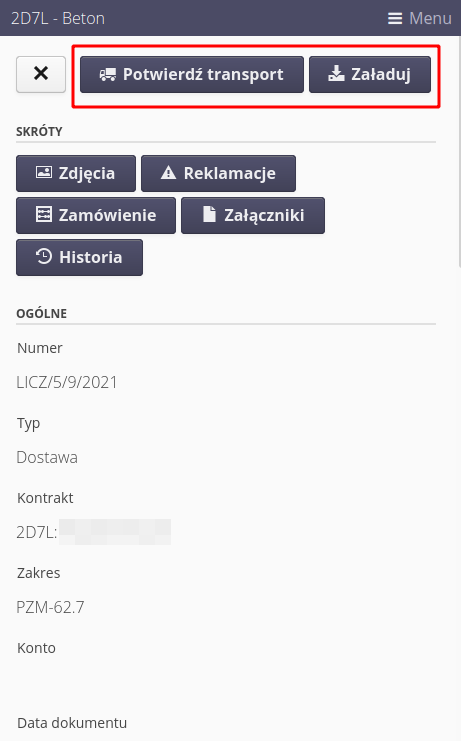
A delivery that is in transit has its own information, but the option to check the delivery is also enabled. This allows you to verify the delivery after it has been delivered to the construction site.
If you have information about the location of the vehicle (from GPS or from the supplier’s IT systems), the system automatically updates the status of the delivery history and the location of the transport. Then you can also direct vehicles to the waiting place, start direct contact with the driver (phone/SMS). |
These data are available in the context menu of the delivered delivery. After selecting this menu from the delivery list, we get the following options:
-
redirecting the vehicle to the waiting queue - the driver receives information via SMS with a link to the supplier’s portal indicating, for example, the route and the place of stop
-
calling a vehicle from the waiting queue - as above with information about the destination place of unloading
-
indication of the vehicle’s location on the map (if we have current information from the vehicle)
-
making a phone call/SMS to the driver
-
changing delivery status and checking times
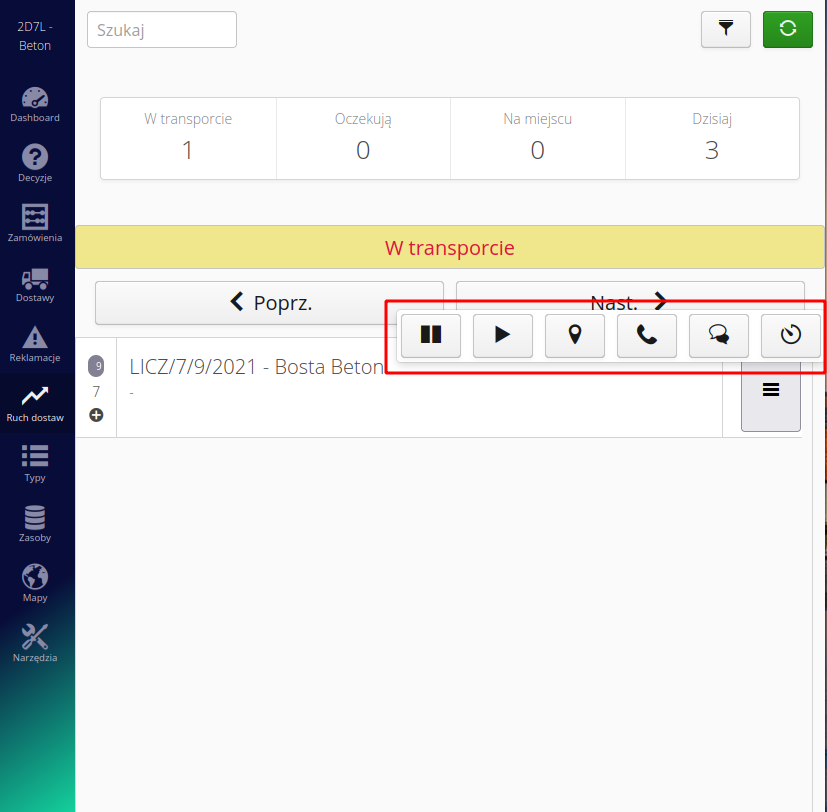
After starting the unloading of the vehicle, we activate the delivery check.
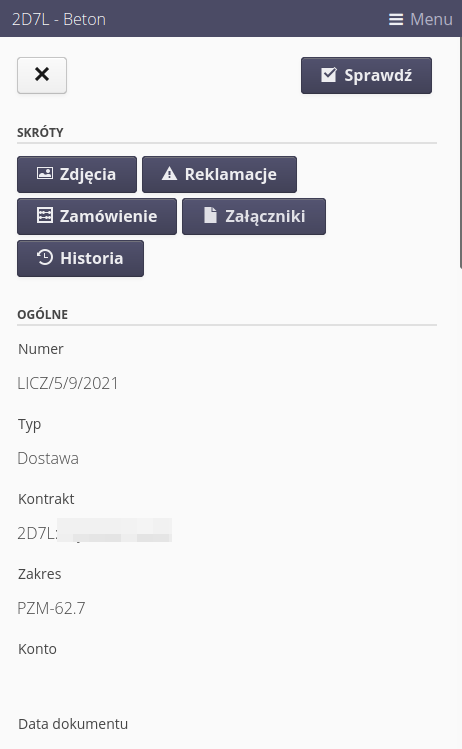
The check allows you to correct the delivered quantity, change the assortment, specify the target structural element (if it has not been previously defined or has changed), prepare photographic documentation and enter the signatures of the deliverers.
While checking the delivery, we can create discrepancies and automatically generate a complaint to the supplier. |
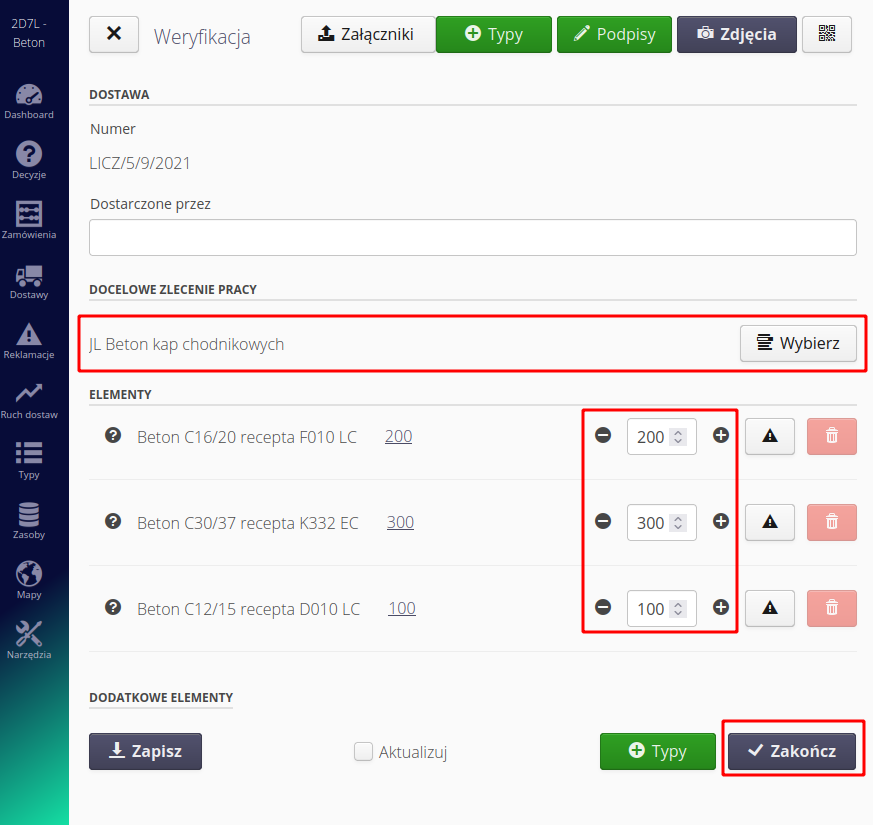
The system automatically records a delivery check every 30 seconds. This allows you to avoid deleting data in the event of e.g. network or communication failure. |
After confirming the delivery (and having the warehouse module turned on), the system allows you to enter the material into the construction warehouse and monitor transports and deliveries. If the order is associated with a given warehouse, it is selected automatically, if not, the user selects the warehouse to which the delivered material is to be delivered.
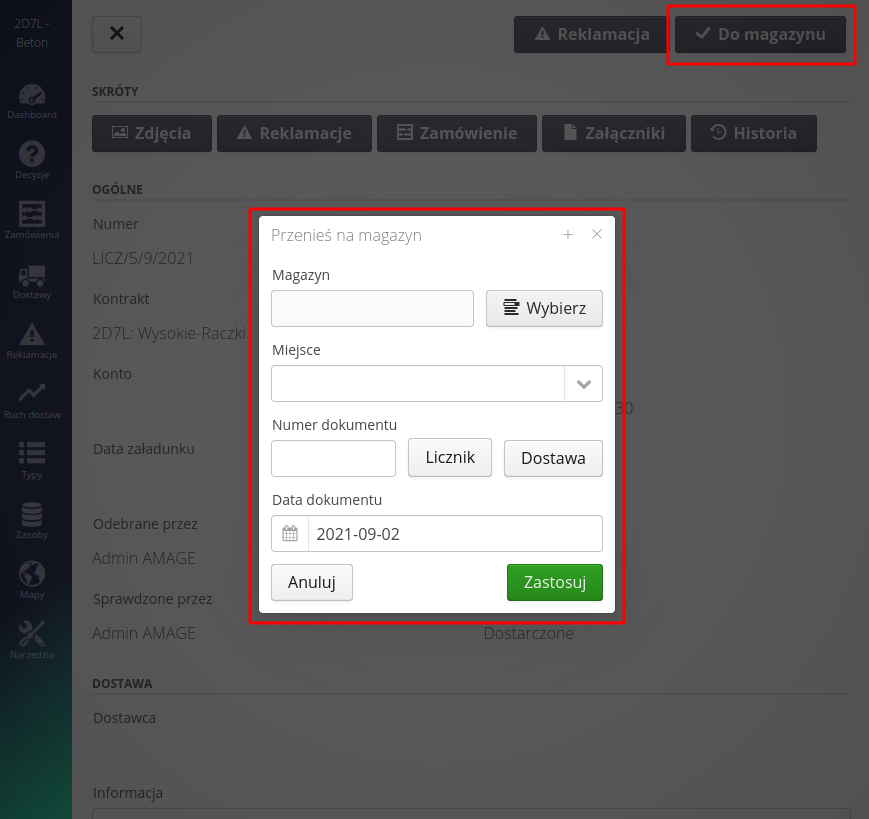
Warehouses in the system serve as actual building site warehouses. They are not warehouses from a formal (accounting) point of view, although they have all their features (documents, turnover, stocks, prices, etc.). The warehouse can determine the actual construction status and the history of all materials on the construction site. |
After the delivery is completed, we can (if we do not have systems tracking vehicles on an ongoing basis) enter key information regarding the delivery, i.e. delivery date, construction time, unloading time.
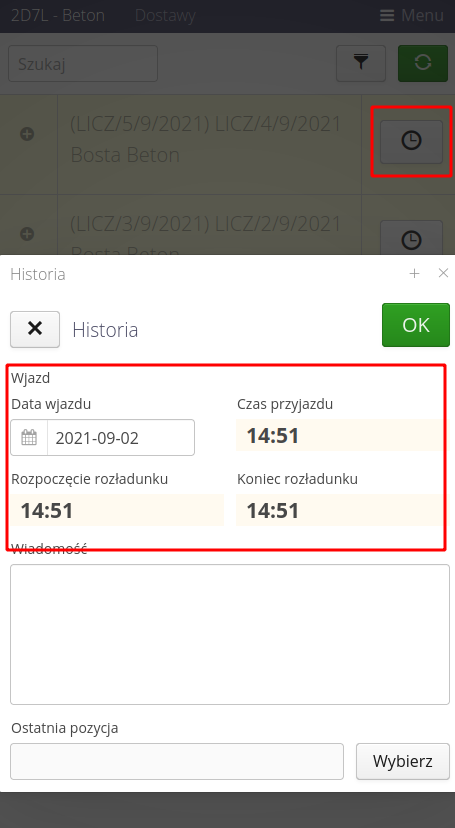
On the basis of this, the transport history is entered and all necessary times and indicators are calculated.
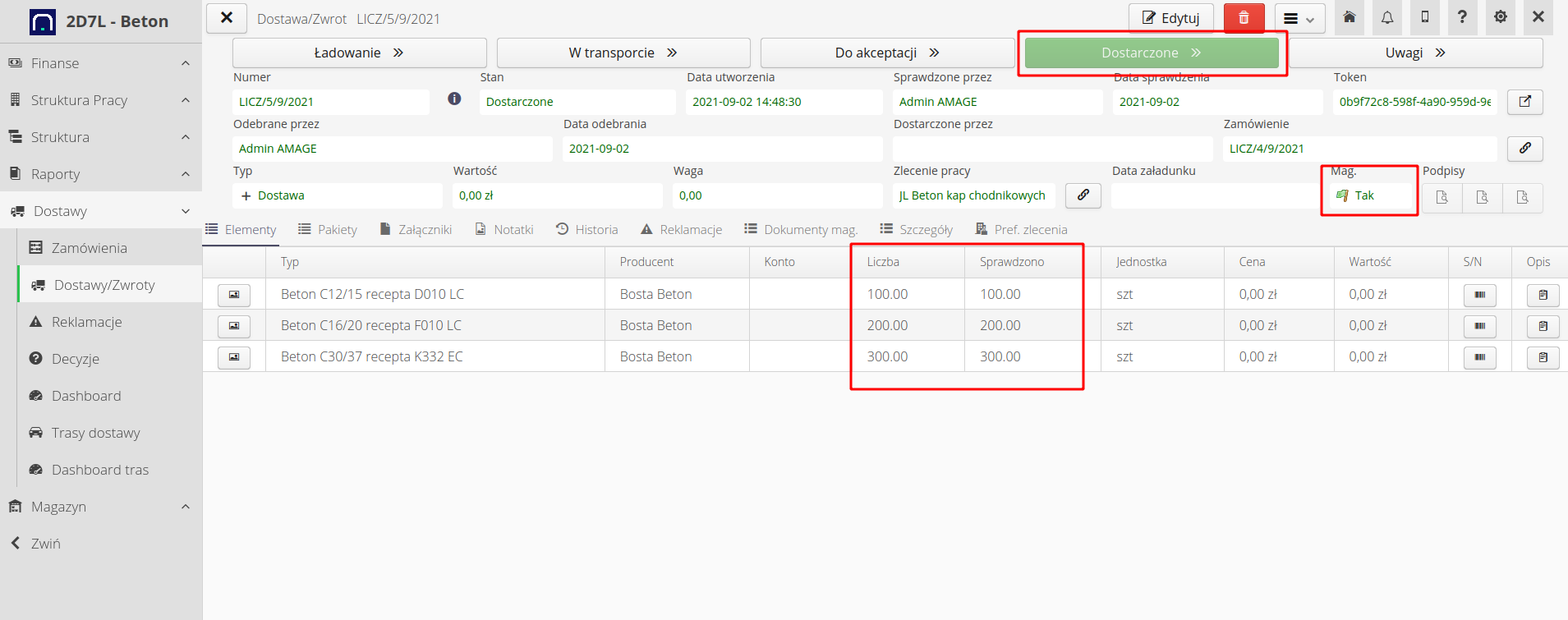
The result of a delivery check is the check information for a specific delivery, its history, and all information related to structural elements.
Delivery time history
The history of delivery times allows you to track the route of the vehicle, waiting history, as well as unloading and departure events. If you have current information about the vehicle’s location, this data is automatically saved by the system. In the absence of this information, the system enters it by a simplified record of these data after completing the delivery check.
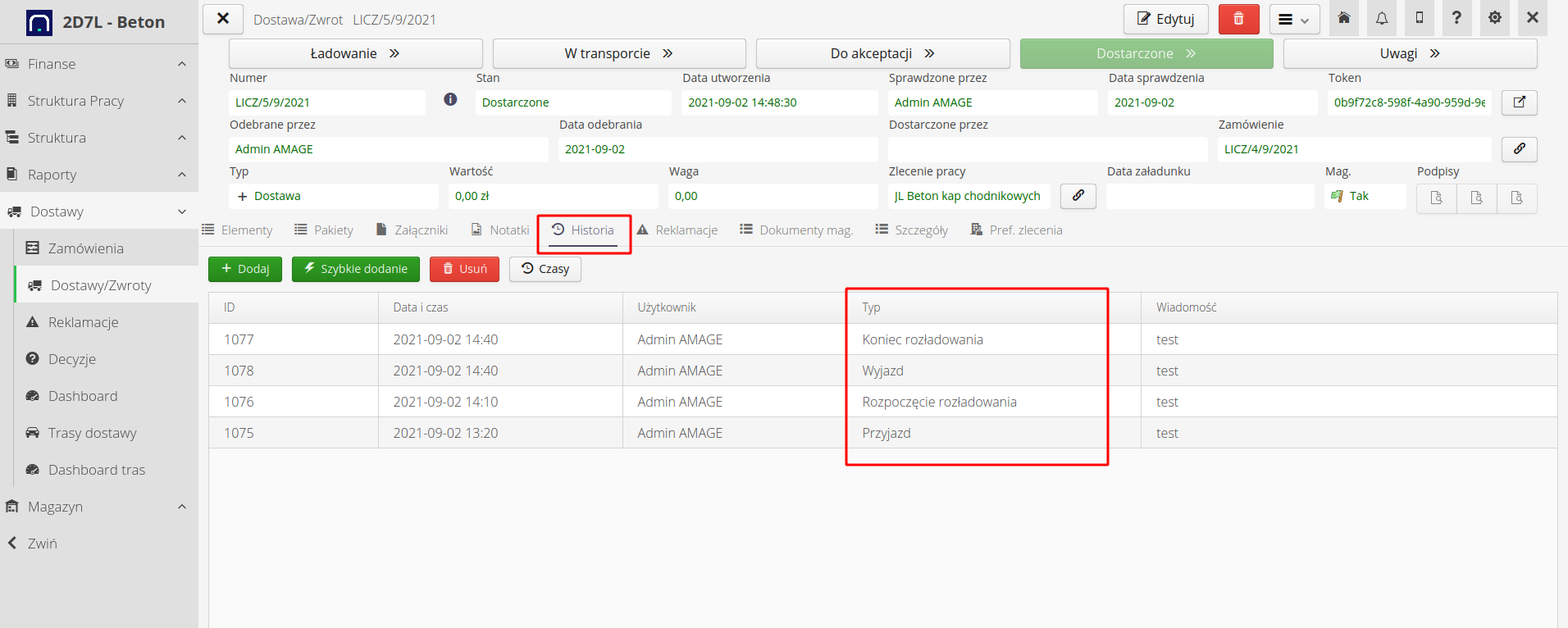
Delivery time status shows all information calculated/saved by the system regarding delivery times.
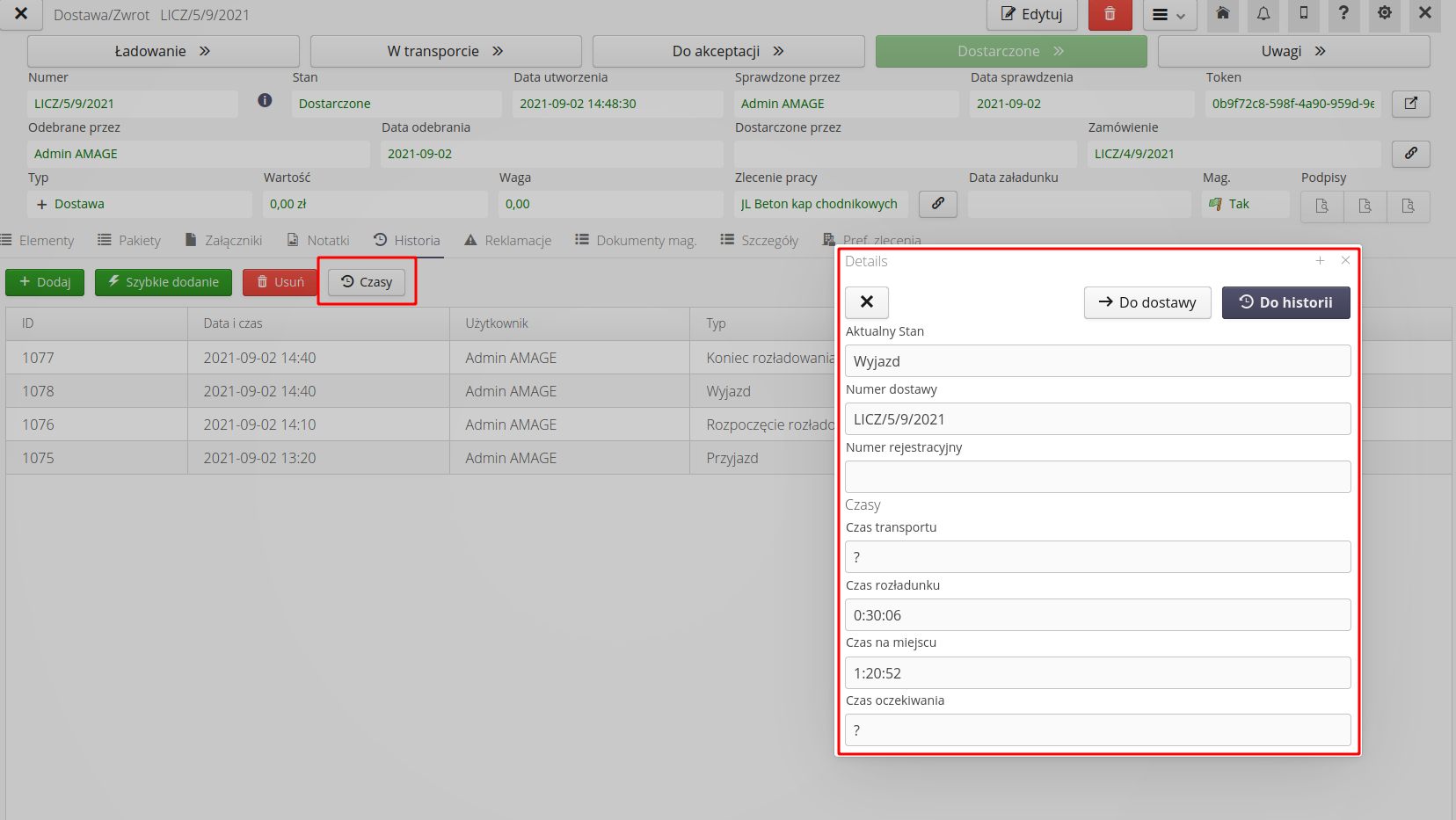
Data analysis and views
During and after deliveries, the system provides a range of information about deliveries.
In the delivery routes view, we can display deliveries in the following contexts:
-
deliveries - shows information about delivery times, dates and statuses
-
orders - shows deliveries compared to orders
-
according to orders - shows information from material plans correlated with orders/deliveries for given structural elements
-
map - displays the current location of transports on the map
-
calendar - displays the events of deliveries in the form of a calendar
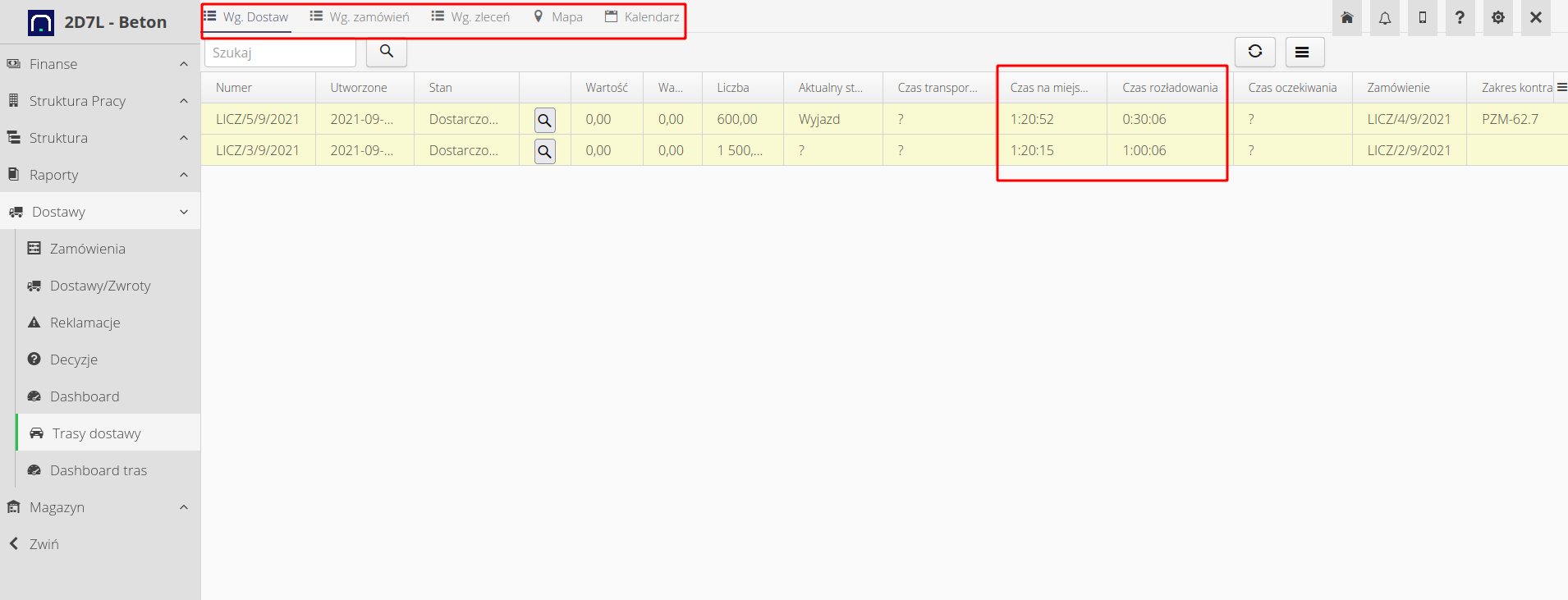
Dashboards are also available that present information about deliveries and vehicles at specific stages (transport, waiting, loading).
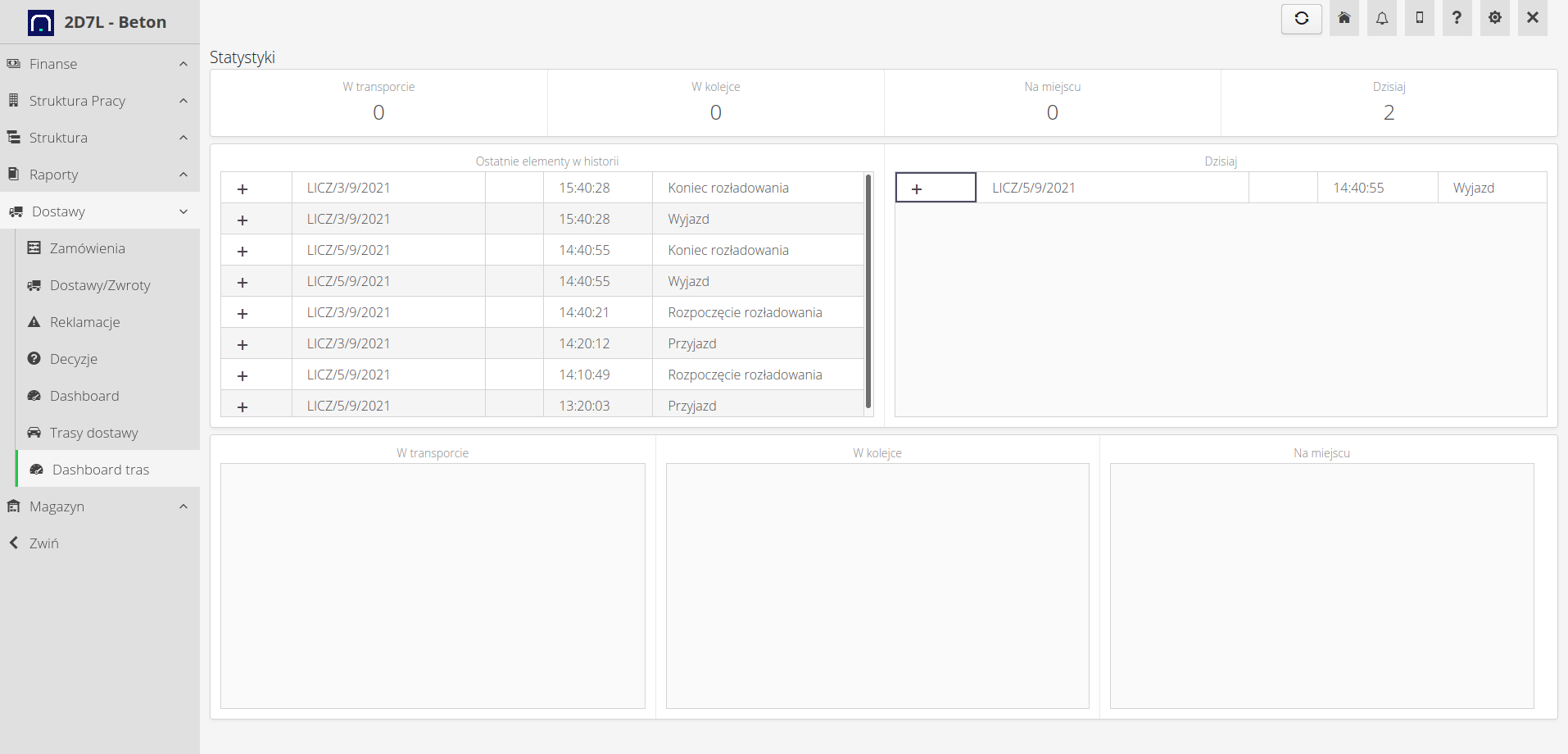
In the mobile view, we show information about transports and provide the opportunity to interact with suppliers/drivers.
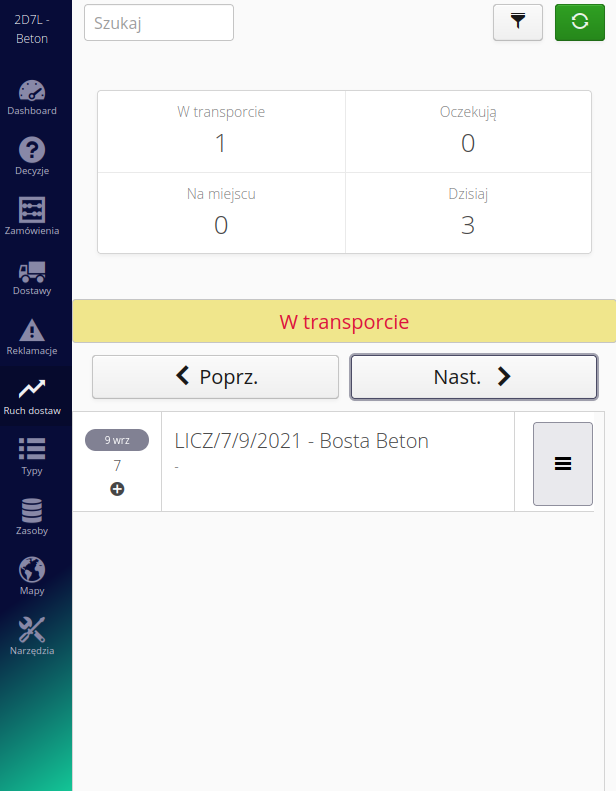
The end result is real information for individual structural elements about material plans and verification of deliveries/orders and internal material turnover.
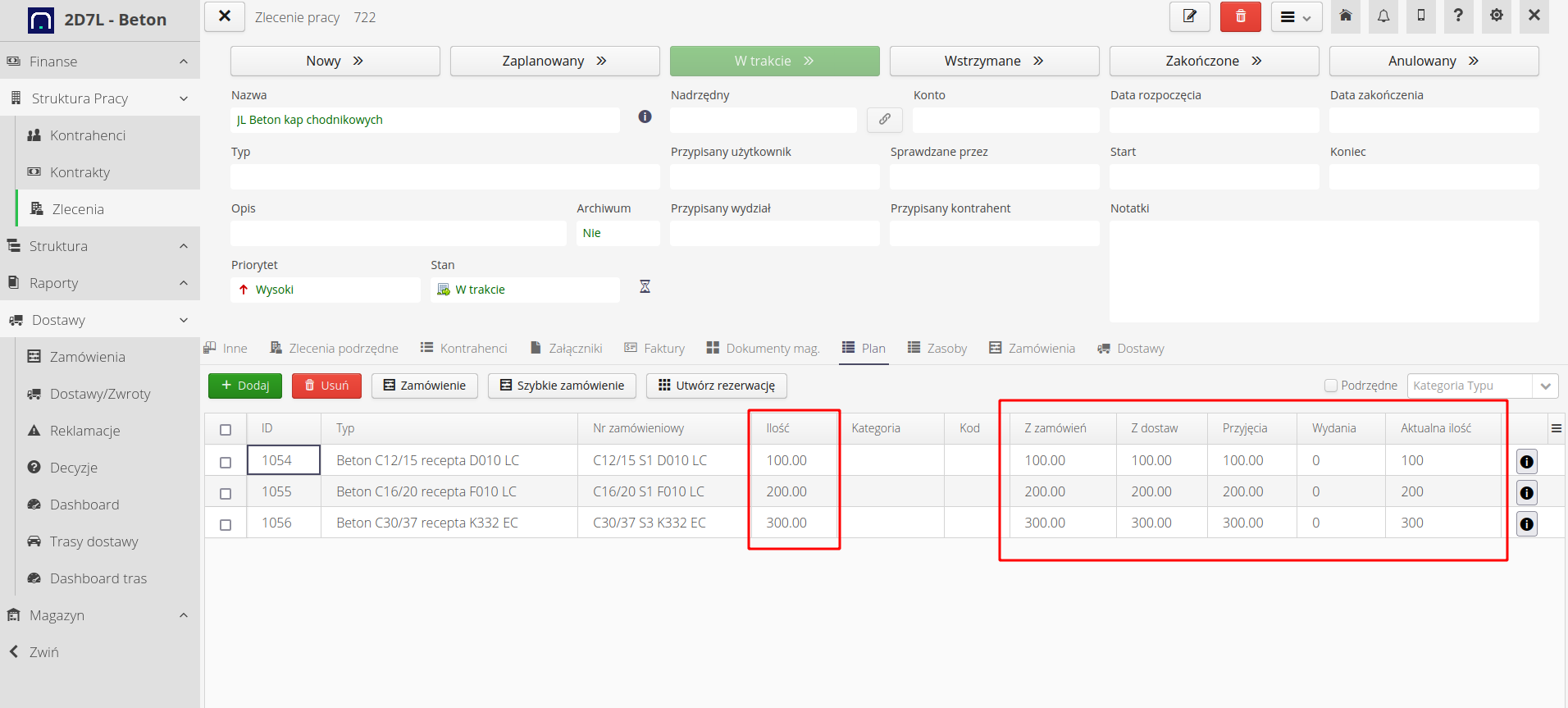
The Howto is based on system version 1.17.0.2 (03.2022) and presents features that may not be available in your system. Ask AMAGE about making this functionality available. |
Due to ongoing development of the system, some screens or configuration files may look slightly different, but will still retain the full functionality described here. This does not affect the core functionality described in this document. |