Deliveries/Returns
Deliveries/Returns
The deliveries/returns view shows information about active (or all) deliveries made within the system. The system allows you to distinguish between two directions of resource circulation:
-
Delivery - the result of ordering from a third-party supplier and making delivery in the Supplier → Customer direction
-
Return - the result of ordering a return from a third-party supplier and executing the return in the Customer → Supplier direction. This case applies, for example, to leased items that must be returned to the Supplier after a period of use.
When selected in the main menu or in context actions (e.g., for an order), all deliveries that are associated with the context are displayed. An action from the main menu displays all active deliveries, i.e., deliveries that have not been delivered or the process canceled.
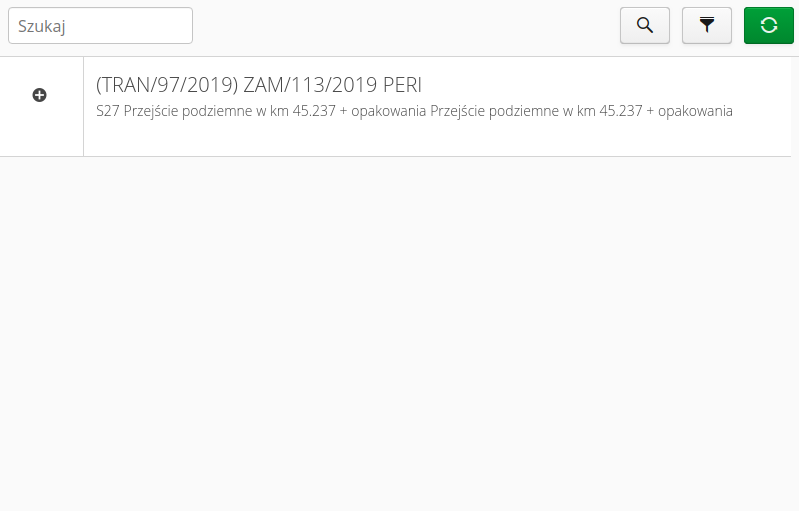
The view displays information about the delivery number, the related order, the type of delivery (+) or return (-), and the related objects and construction elements to which the delivery relates.
The application has the ability to filter the delivery view by displaying a filter (the "filter" button), which displays an additional window where you can select filter criteria:
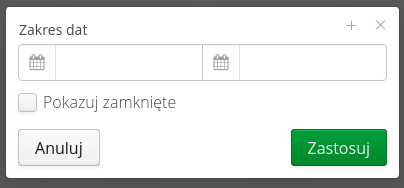
Closed deliveries are presented in a different style than active ones. When a specific delivery is selected, its details are displayed.
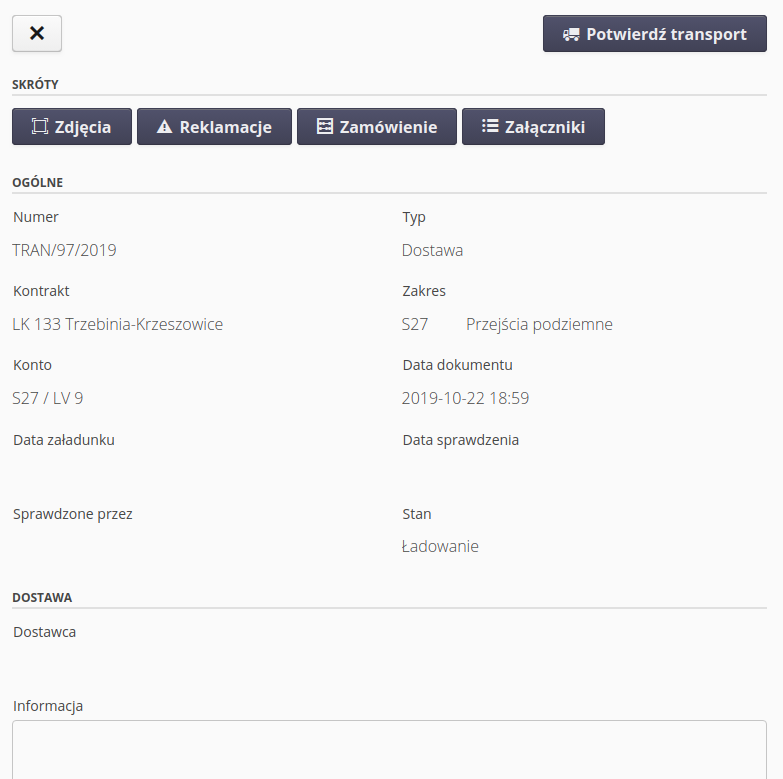
Information of a given delivery, related orders, objects and contract is presented. A list of items ordered with information on status, delivery check. From the list of shortcuts you can go to related service event, the order that generated the given delivery and the list of attachments. The actions at the top of the view are contextual and change from the current status of the delivery.
Create a delivery
Delivery is created on the basis of an order. Delivery can be created:
-
By a system user with appropriate permissions based on the order. Both in the mobile interface and in the extended interface. The user has the option to create a delivery based on information from the order, or create an order by adding items from the assortment.
-
By the supplier through the supplier interface. The supplier for orders enters information about deliveries in progress.
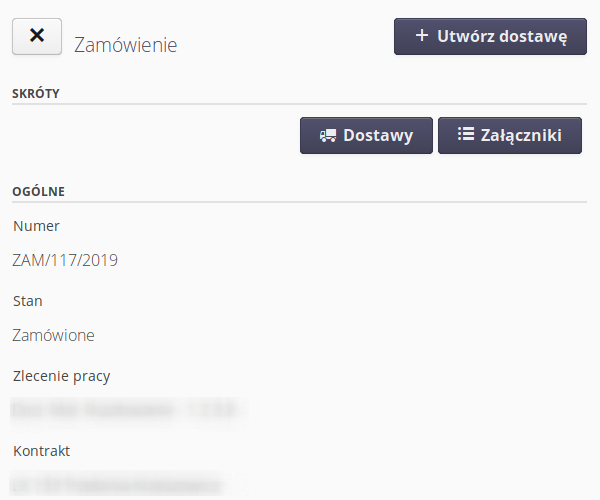
Delivery is divided into two types: * delivery to order - order to a third party supplier and then delivery from supplier to customer * Delivery (return) to the return order - return of items that are leased. The customer’s inventory is returned to the supplier. To implement the return, you must first generate a return order (usually it is required to notify the supplier of the need for return, then, for example, information about the transport that will receive the goods is generated)
Delivery from return is distinguished in the system by type information. In the list of deliveries, you can recognize the delivery by the icon (+) from the return - icons with (-) |
After creating a delivery, depending on whether you have chosen to create a delivery based on an order or create an empty delivery, the system presents a window for adding/defining the quantity of assortment in the delivery.
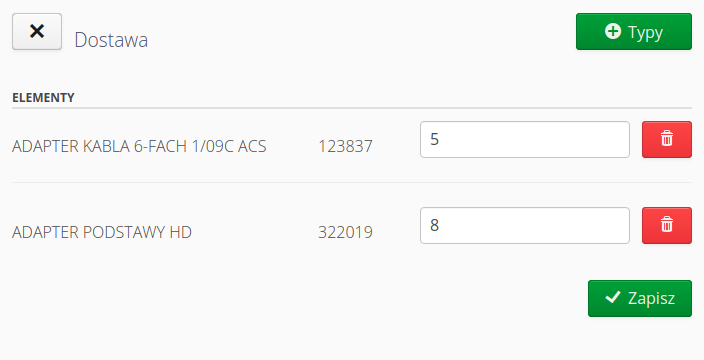
In the view, you can change the quantities of the ordered assortment and through the ''Types'' button, you can add additional items based on the assortment search.
Once approved, the delivery is saved, it receives an initial status and the information defined in the system is generated (e.g., email information about the creation of the delivery, transfer of the delivery to the external supplier’s system, etc.).
The delivery procedure can be further limited by an approval or confirmation process. This depends on the system configuration. Acceptance is realized by the decision module and email notifications. |
Loading the delivery
In the case of return delivery, the first step is to create a return order. At this point, the supplier gets a notification to arrange transportation for the leased items. Once the delivery is made and the vehicle is delivered to the construction site, loading takes place
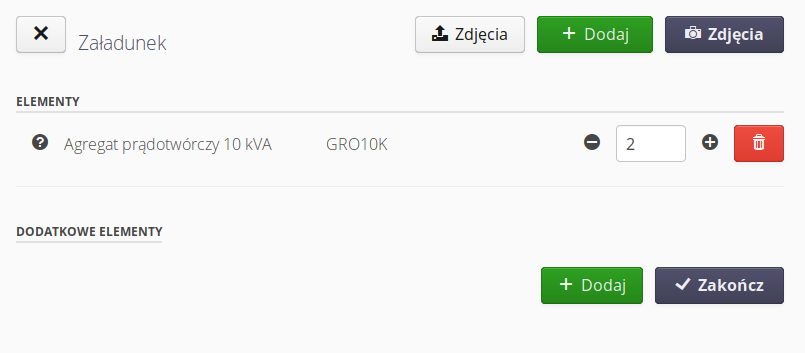
Since deliveries (not returns) are loaded by the Supplier in-house, this step is not included for this delivery. |
During operation, the system automatically saves the current status of the elements in the background. The recording is carried out every 30 seconds. The user is presented with the 'Saved' message at the bottom of the screen at this point. |
Delivery check
Once the delivery/reimbursement is delivered to its destination, the delivery verification procedure takes place. This involves counting the delivery, creating photo notes, creating claims, approving with signatures, and forwarding the information to order coordinators for stock entry.
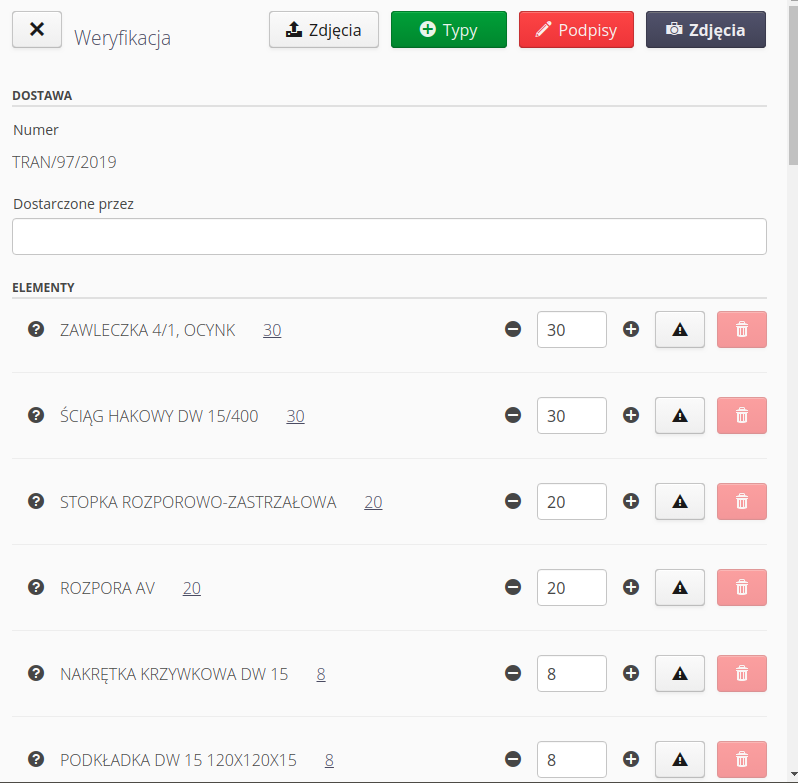
The delivery check window presents a list of assortments declared for delivery within a given delivery. The information is presented in the form of a list with information about the type of assortment, the quantity declared, the current quantity, a claim control, a delete assortment button. In the main part, information about the delivery number, delivery person (e.g. driver) appears. Selecting the button (?) will display a photo of the assortment (if it has one). Selecting (pressing) the declared quantity will enter this quantity into the current quantity control.
In case you want to enter a claim, you have this option through the button with an exclamation mark. Selecting this button displays an additional control with the possibility of entering a value for the complaint. Complaints are divided into quantity and quality complaints.
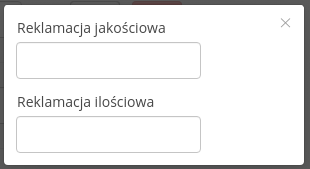
Entering a value in the quantity control that does not correspond to the declared quantity will automatically result in the appropriate indexation of the quantity claim. |
After entering a claim, the claim opening button will turn red. This means that a claim has been entered for the assortment.
Entering a claim during a check does not immediately generate a claim. It is created at the end of the check after the user confirms it. |
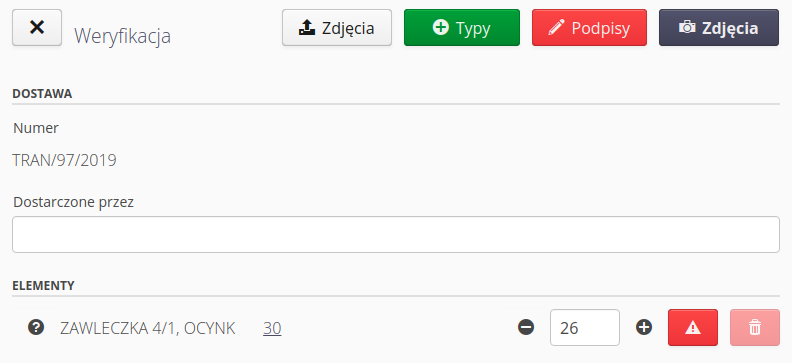
The delete assortment button is disabled during a normal check. To enable the assortment to be corrected during check execution, edit mode must be enabled. This is available in the action bar at the end of the list.
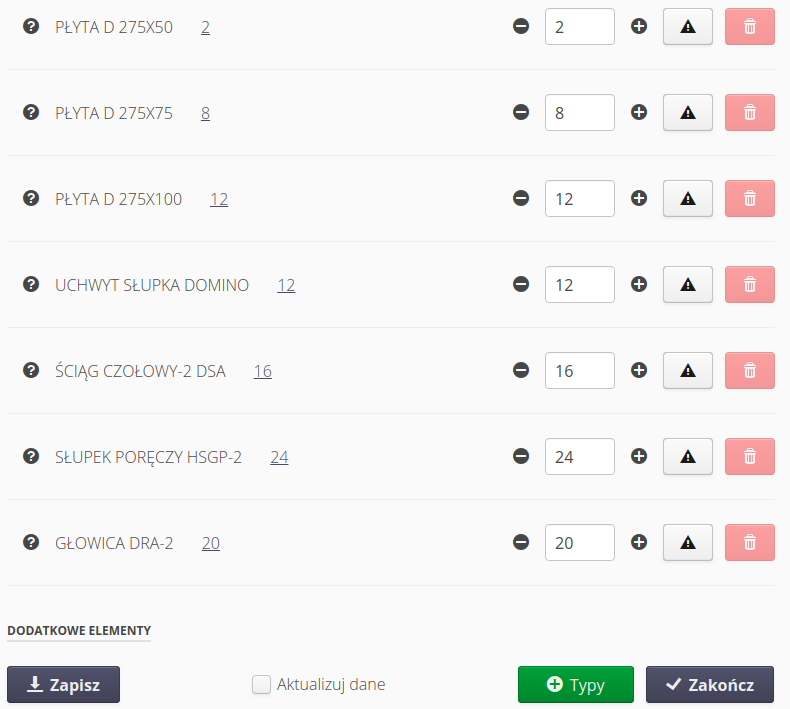
Actions are available in the bottom bar:
-
save - saves the check BUT DOES NOT END THE PROCEDURE. This allows you to save a partially executed check and return to the check at a later date. All fields and information are saved in non-volatile memory and are restored when the check is opened again.
-
update data - enabling this option will allow you to delete individual assortments (the "garbage can" buttons will be enabled). The editing of the delivery number will also be enabled. This can be used to enter the number of the actual delivery provided by the supplier (usually, the delivery number is provided on the waybills only when the delivery is present at the destination).
-
types - the ability to add additional items that appeared in the delivery. Only for deliveries (not returns).
Touching/clicking on the assortment name will lock the row in question. This allows you to selectively lock for editing items that have already been checked. This makes it easy to see what is still left to check. |
The user is required to enter the signatures of those performing the check. This is realized through the "Signatures" button. A description of this window is included in the general part of the documentation. The button for adding photo notes and the procedure is also described in the general part of the documentation.
Deliveries - at the time of checking, the person receiving the material enters the signature. If the signature is inserted, then this is the one who was checking. If there is not, then the system goes to the mode of acceptance of the delivery by the coordinator.
If any quantitative or qualitative complaints have been entered then the user will be notified of this, and once this information is approved, the delivery is automatically closed, along with the creation of a complaint based on discrepancies during the delivery in progress.
During operation, the system automatically saves the current status of the elements in the background. The recording is carried out every 30 seconds. The user is presented with the 'Saved' message at the bottom of the screen at this point. |
In the case of systems that have parameterization and item identifiers in stock enabled, an additional context menu appears in the view for each item. After selecting it, we can enter the parameters of a given delivery and the identifiers of the received or issued materials.
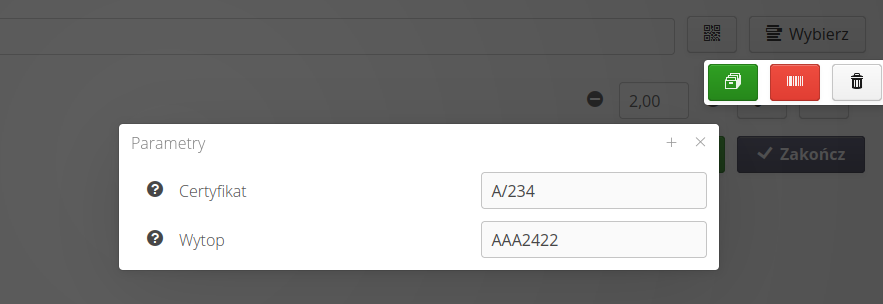
Refer to the main application documentation. The storage section explains these features in detail. |
Deferred acceptance of delivery check
If the verifying person is not available during the delivery, you can skip entering his signature. If the application detects that there are only the signatures of the persons of the supplier and the verifying person, it will set the status "For verification" for the delivery in question at the end of the check. This allows the delivery coordinator to verify the correctness and accept it at a later date.
Stock entry
If the user who performs the delivery check has the authorization to enter the document into the warehouse then the system displays a query after the check is completed whether to enter the items into the warehouse. After confirmation, the warehouse entry window is opened. The user can select the document numbering format and the date of the document entry into the warehouse. Once approved, all other operations are performed automatically.
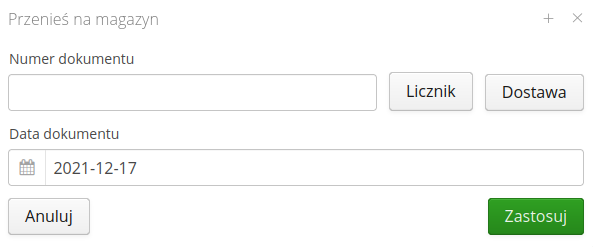
The system automatically checks for duplicate assortments in the delivery list when entering a document into the warehouse. This can happen when a supplier/user declares the same assortment several times in a delivery. This is allowed, but during the warehouse entry these items are combined (summed) to one entry. In this case, the system displays the information Duplicates found. Should they be merged into single entries?
. If the user selects Repair myself
then the system returns to the delivery check view and allows manual correction. If he selects Merge
the system will automatically merge the duplicate assortment.
This operation is unavailable if inaccuracies, i.e., quantity/quality complaints, are detected during the delivery check. In this case, the system will not ask you to enter the document into the warehouse and instead will allow you to create a claim. Entry into the warehouse will already be possible directly from the Desktop interface. |