Monitor work reporting on work order
Introduction
The document shows the possibilities of reporting performed works in work orders. After enabling detailed reporting of the work performed, the system presents forms during the change of their status that allow you to record the time worked, the scope of work, the participation of people in the brigade and the materials used.
Task
A work order in the AMAGE system allows you to monitor the work performed under the order. When changing the order status to "In progress", the system presents a form that allows you to report on the work performed. We will report the completion of work in the "March Project" order.
Implementation
Work orders allow for detailed reporting of work progress and material used. These are two dimensions of reporting. One is the amount of work that needs to be done in the task, e.g. laying 30 m of cable route, and the other is the elements that were taken from the warehouse to perform this activity.
For example, we may log 30 m of work done and take 1 piece of a 30 m long route element or 10 pieces of a 3 m long route element. We can measure the work done in two dimensions. One of them is the time spent working on the order and the other is the workload depending on the order and activity.
A separate element is the list of materials necessary to perform the work in the order, which we can compare with the actual consumption of materials reported by employees.
For example, reporting on these activities may look like this.
The screens show the work order reporting mechanism directly from the system’s desktop view. The same mechanism works identically for the mobile view. The only difference is reporting in the mobile view to orders that have been assigned to a given person, e.g. a foreman. This facilitates work in the field, where the employee does not have to look for orders that are not assigned to him. |
We select the work order we want to analyze.
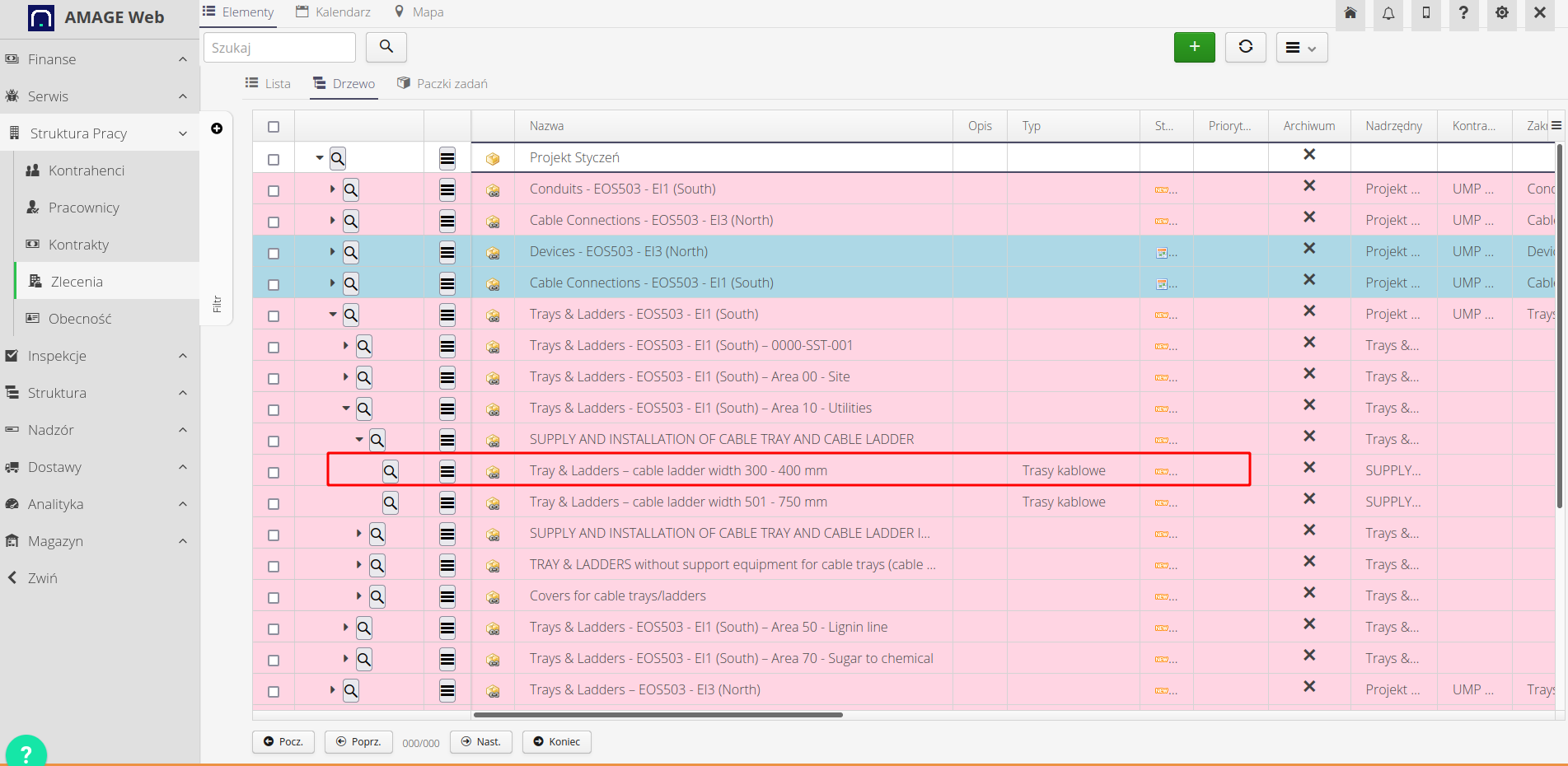
In the work order view, in the 'Other' tab, we have data regarding, among others: work dimensions and required materials. In this case, we have 282 hours of work planned and 240 hours of work to be reported. Due to the type and description of the task, we know that it is 240 m of laying cable routes.
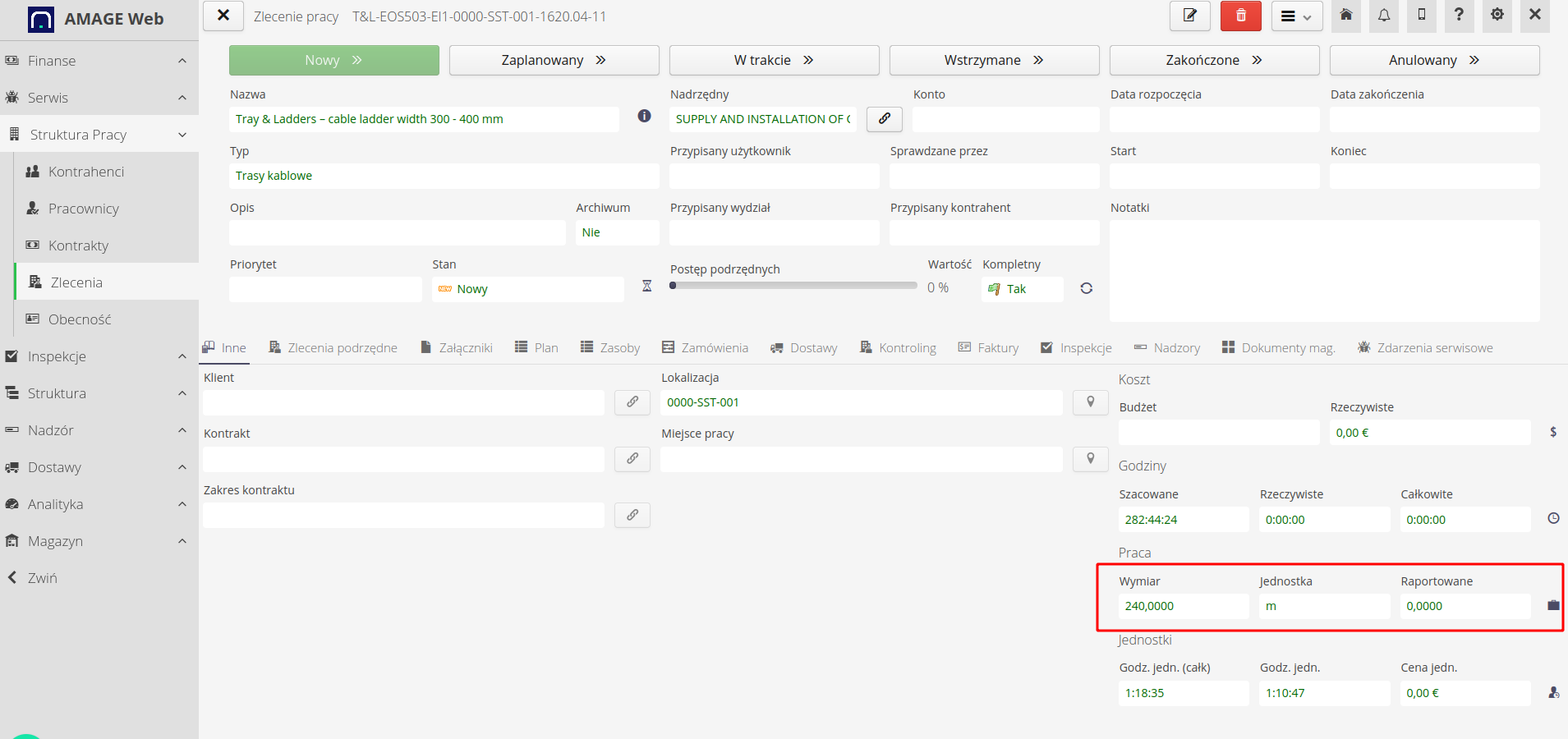
However, a separate thing is the material list resulting from the project. It specifies the material necessary to be taken from the warehouse to complete a given order. It may result from the material list from the project, from the assortment or from the warehouse.
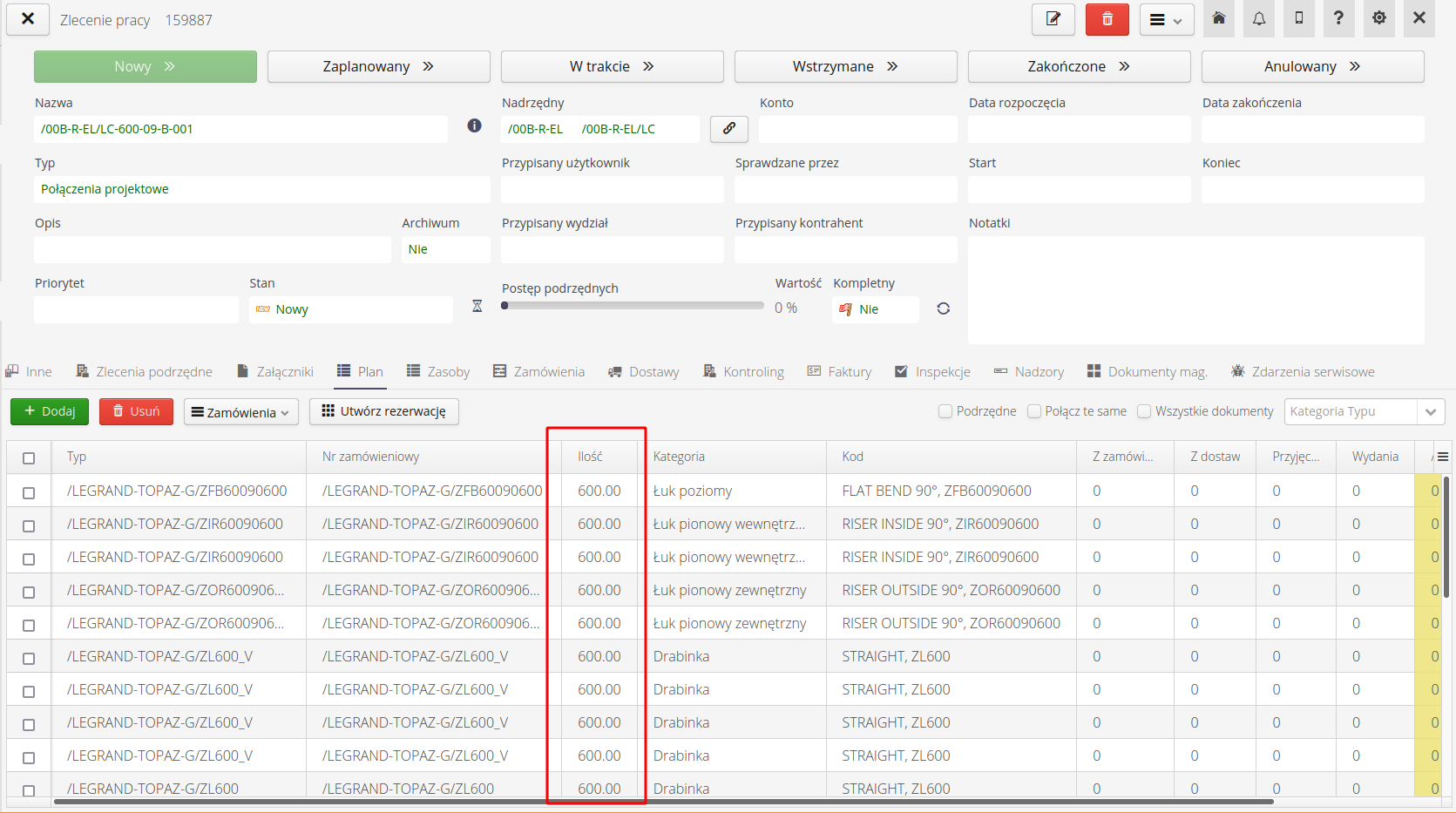
Reporting involves entering information when the order status changes. When the order status changes to Suspended
or Completed
, the data logging interface is expanded to include reporting of all these indicators. In this case, we report using access to the work order history. There is an 'Add' button here that allows you to add a new history entry. When the status changes, we can report the amount of work, i.e. how many meters of the route I have laid today. Here we entered that we laid 34 meters, without specifying how many pieces of source material it was. Using this mechanism, we can monitor the assumed dimension (offer/project) and implementation.
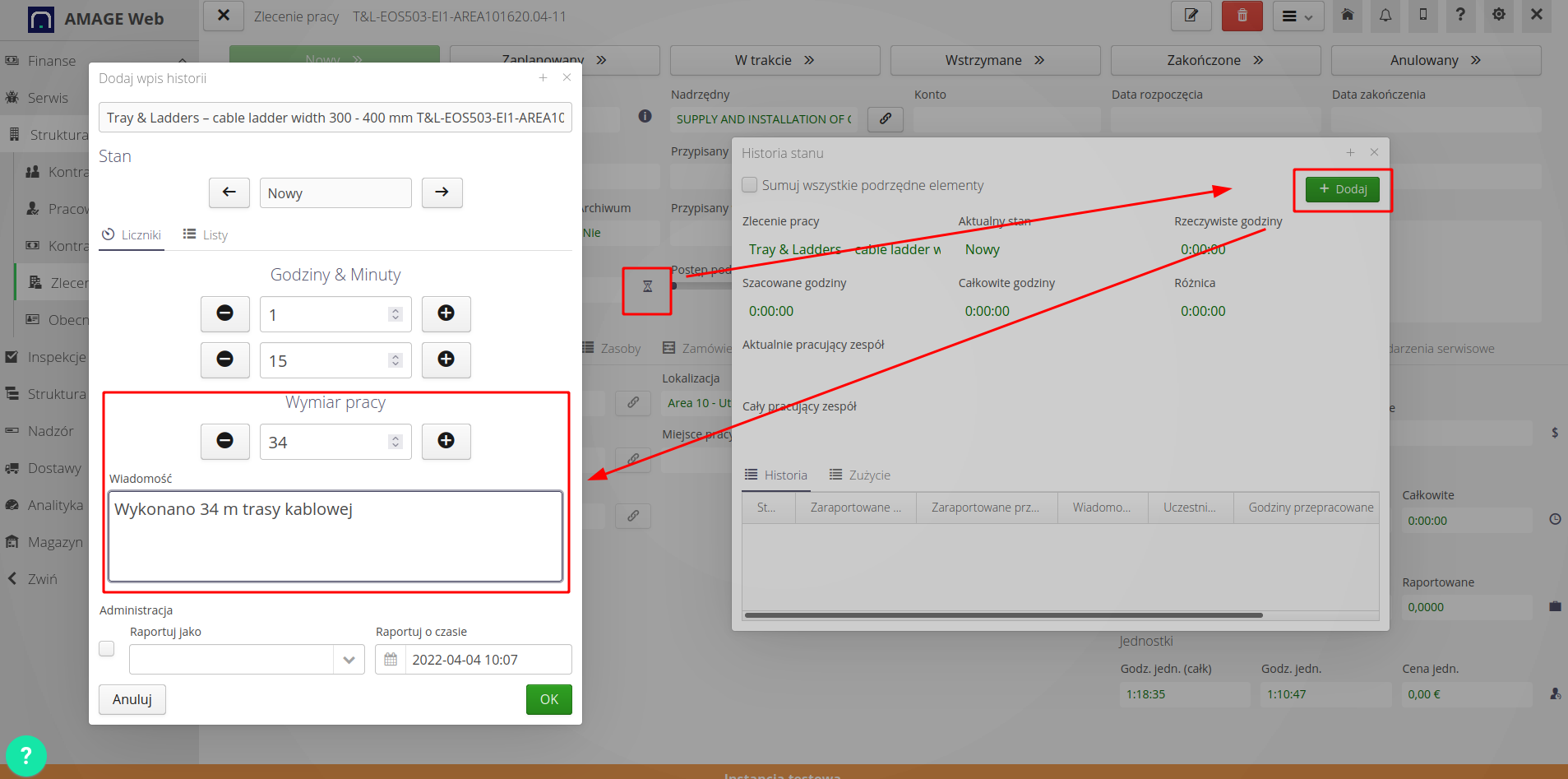
If a user has super-administrator rights, he or she can enter historical data for other users. Therefore, in this view we have a part of the interface that allows you to enter data for a selected person and at a selected time. Sometimes it is necessary to complete data in the system when the reporting person is, for example, absent from work. |
Material reporting is a separate scope. We choose exactly what material we used. Reporting is available in a separate tab of the progress reporting dialog. In the Materials
list we have a list of elements that were used during work.
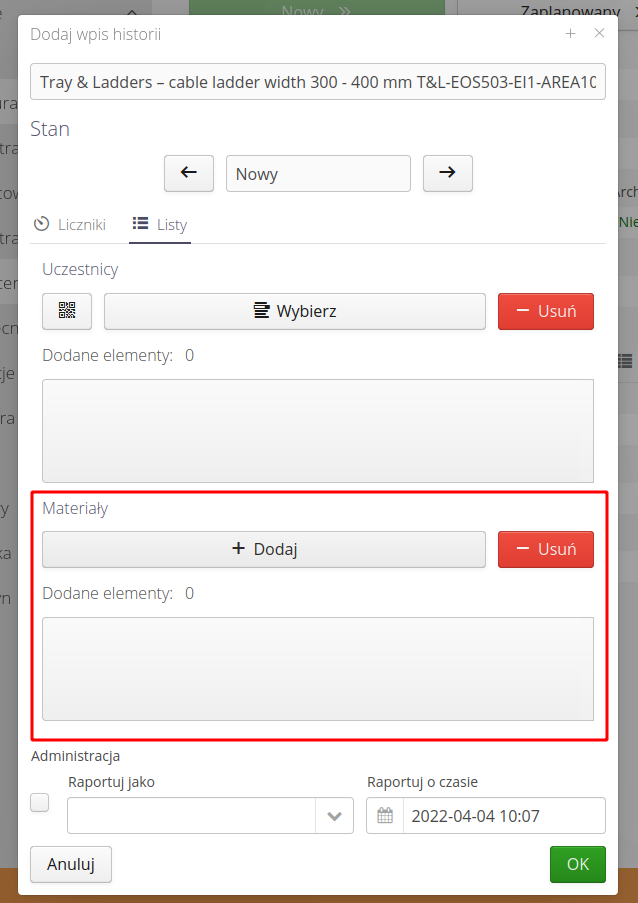
When we select the 'Add' action, we can add material from several sources. Project → select elements from the project material list. We simply select the types from the range available globally in the application. Warehouse → here we show the assortment that was issued via release documents for a given order from the warehouse. In this case, we report by selecting materials from the warehouse. We select the material and enter the quantities.
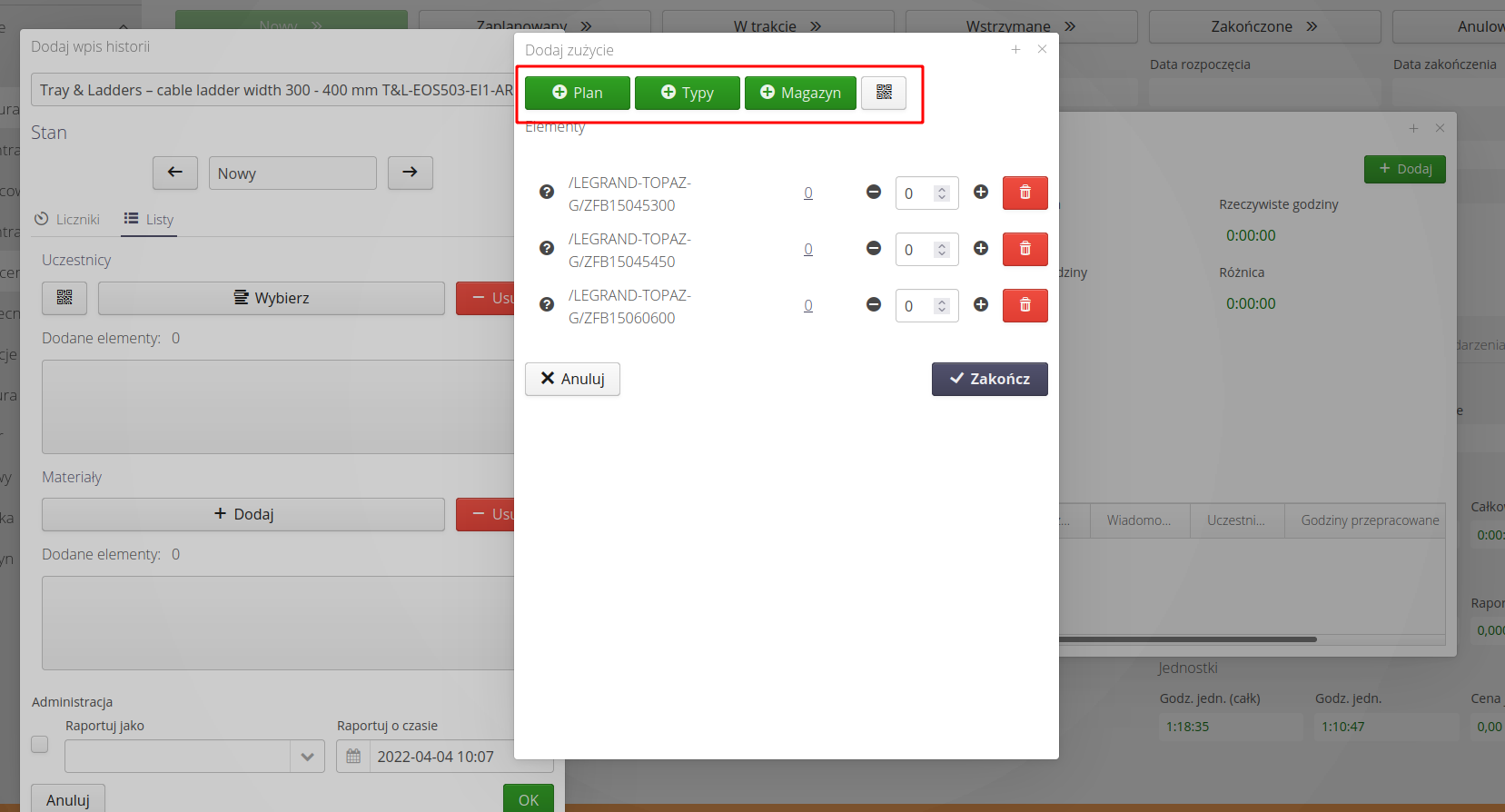
We save the data along with additional information, e.g. a list of people participating in the order - the composition of the brigade.
As a result, we receive the saved data:
-
Materials issued for this order with specific quantities
-
Reported work size, i.e. 34 m of cable route with recording time
-
Reported work time on the order is 1 hour 15 minutes
-
People participating in the order
All this data is used for additional analysis and verification of progress and work efficiency.
Summary
The AMAGE system allows for detailed reporting of work performed in work orders. When changing the order status to 'In Progress', the system presents a form that allows you to report on the work performed. All data is used for additional analysis of the work being carried out.
The Howto is based on system version 1.17.0.2 (03.2022) and presents features that may not be available in your system. Ask AMAGE about making this functionality available. |
Due to the ongoing development of the system, some screens or configuration files may look slightly different, but will still retain the full functionality described here. This does not affect the essential functions described in this document. |